A Guide to CNC Machining for the Medical Industry
Upload Time:
Sep 29, 2023
CNC machining has become an increasingly popular technique in the medical manufacturing industry due to the high demand for precise components. These components need to meet strict quality and safety standards and be produced efficiently. Therefore, product designers and manufacturers have embraced medical CNC machining as a solution to meet these requirements. The medical industry benefits greatly from the versatility and compatibility of CNC machining. It serves as an ideal manufacturing option due to its ability to effectively produce medical components with exceptional precision and accuracy. By utilizing CNC machining, the healthcare sector can ensure the safety of patients and minimize the occurrence of errors. In this article, we will overview the role of CNC machining in the medical industry, common materials suitable for medical device parts machining, considerations for materials selection, and tips for optimizing the CNC machining of medical parts.
- The Roles of CNC Machining in the Medical Industry
- Common Materials Available for Medical Instrument Parts Machining
- Factors to Consider When Selecting Materials for CNC Machining Medical Parts
- How to Optimize Your Medical CNC Machining Projects
- Conclusion
- Your Reliable CNC Machining Expert in Medical CNC Machining – Dedasun Tech
The Roles of CNC Machining in the Medical Industry
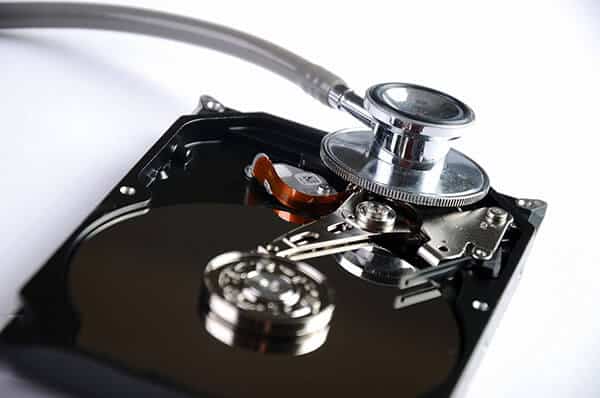
The healthcare sector relies on CNC machining to produce medical prototypes and components that require tight tolerance and performance standards demanded by the industry. There are several reasons why CNC machining is extensively used in the medical field:
1. No limitations on quantities
When a CAD file is created, it can be quickly converted into a coding program. This coding program enables the production of numerous parts with a simple button press. This capability is particularly advantageous in the medical industry, where the production of specialized devices, equipment, prosthetics, and other components often involves custom, one-off manufacturing. Being able to easily manufacture single-use or custom parts is a significant benefit in this context.
2. Suitable for urgent applications
The time required to transform a digital CAD file into a finished product using CNC machining can be as little as a few hours, depending on the complexity of the medical component.
Fast manufacturing through CNC machining is highly dependable, especially in urgent medical situations where the types and quantities of supplies are difficult to predict. These time-sensitive supplies could be critical for the treatment of future patients within a narrow timeframe.
3. Tight tolerance
Decent CNC machines make it easy to achieve the extremely tight tolerances required by many advanced medical devices. CNC machining ensures exceptional surface finishes and requires minimal post-processing.
In the medical field, equipment, devices, and products must be suitable for their intended purposes. Severe consequences may occur due to any variations in specifications. However, digital machining significantly reduces this risk to an absolute minimum.
4. Not require specialized tooling
CNC machining is viewed as a cost-effective and efficient approach to manufacturing precise medical components without the need for specialized tooling. Unlike other production methods, this process virtually doesn’t require expensive tooling, resulting in significant time and cost savings.
In contrast to the time-consuming process of creating dedicated mold tooling, which can take up to four weeks, precision CNC machining can make custom parts or small production runs at a fast turnaround. This is particularly advantageous in the medical industry, where there is often a need for rapid and accurate production of parts in limited quantities. CNC machining serves as an ideal solution to deliver precise and high-quality results without the necessity of specialized tools.
5. Flexible digital programming
The ability to swiftly and effortlessly transfer digital programs between product designers, medical specialists, and manufacturing professionals is a notable advantage of CNC machining. This seamless exchange greatly enhances its effectiveness in producing specialized and high-quality CNC machined medical equipment, regardless of geographical location. This advantage proves particularly valuable in time-sensitive situations, enabling the rapid creation and delivery of crucial medical components.
6. Materials versatility
Standard CNC machines can handle the prevalent materials preferred in medical and surgical tools, appliances, and devices, such as titanium, stainless steel, aluminum, and production-grade plastics like PEEK. Digital machining enables the utilization of portable CNC machines and the seamless transfer of digital CAD files. Portable CNC machines, although having limited capacity, facilitate the production of simple medical components.
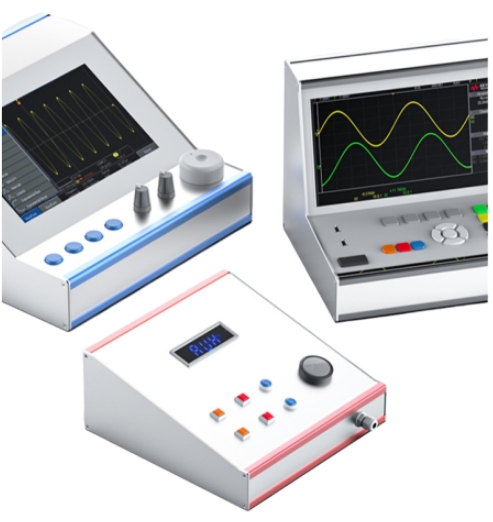
Common Materials Available for Medical Instrument Parts Machining
When designing medical components, factors such as tolerances, malleability, and tension requirements are typically taken into account. Additionally, considerations are made for disposal and sterilization requirements. Hence, it’s imperative to select materials for CNC machining that fulfill both functional and quality requirements.
Stainless steel is the predominant material used for manufacturing medical devices, although titanium and aluminum are gaining popularity. In certain situations, plastic polymers and certain composites are also suitable choices.
The following tables provide a summary of common materials available for medical CNC machining:
Metals
In the medical device industry, the ideal metals for machining possess inherent corrosion resistance, sterilization capability, and ease of cleaning. Stainless steels are widely utilized due to their non-rusting properties, machinability, and minimal or no magnetic characteristics. Certain grades of stainless steel can also undergo heat treatment to improve hardness. Alternatively, materials like titanium provide excellent strength-to-weight ratios, making them advantageous for implantable, handheld, and wearable medical devices.
Materials | Properties |
Stainless Steel 304 | Stainless steel 304 is a commonly used alloy in various applications, thanks to its excellent combination of corrosion resistance and machinability. However, it cannot be heat treated to enhance hardness. In cases where hardening is necessary, it’s advisable to opt for 18-8 stainless steel. |
Stainless Steel 316/L | Due to its exceptional corrosion resistance, stainless steel 316/L is widely favored in the medical device industry. |
Stainless Steel 15-5 | 15-5 stainless steel provides corrosion resistance comparable to that of stainless 304, while also offering high corrosion resistance, improved hardness, and workability. |
Stainless Steel 17-4 | Stainless steel 17-4 is a corrosion-resistant stainless alloy known for its high strength and heat-treatability. It is commonly utilized in medical equipment applications. |
Titanium Grade 2 | Titanium grade 2 is a highly pure, non-alloy material known for its low weight, high strength, and thermal conductivity. |
Titanium Grade 5 | Ti-6Al-4V, known for its excellent strength-to-weight ratio, owes its enhanced strength to a high aluminum content. This widely utilized titanium alloy offers favorable attributes such as high formability, corrosion resistance, and weldability. |
Aluminum | Aluminum is a lightweight and durable material with favorable corrosion resistance. It can also be conveniently anodized to enhance mechanical properties and corrosion resistance. While it may not be the most suitable option for devices that come into direct contact with the human body, it is ideal for support equipment such as orthopedic supports, IV stands, wheelchairs, and other similar applications. |
Copper | This metal is known for its exceptional antibacterial and antiviral properties, making it well-suited for frequently touched surfaces such as monitor switches and buttons. It’s sometimes also utilized in certain dental implants. |
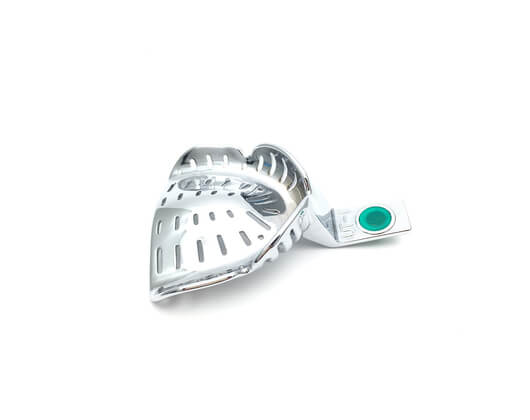
Plastics and Composites
Plastics commonly used in medical devices have desirable attributes, including low water absorption (moisture resistance) and excellent thermal properties. These materials can typically undergo sterilization through methods such as ethylene oxide treatment, autoclaving, or gamma irradiation. In the medical industry, low surface friction and improved temperature resistance are also highly valued. Plastics are often employed as alternatives to metals in applications like guides, housings, and fixtures where factors such as magnetism or radio frequency interference could potentially affect diagnostic results.
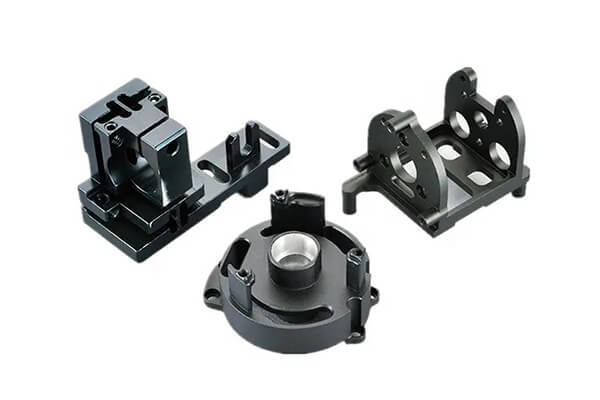
Materials | Properties |
Acrylic | It’s known for its impact resistance and optical clarity. It is commonly used for machining medical components such as protective shields, contact lenses, orthopedic implants, microscopes & lasers, and dental prosthetics. |
Nylon | This engineering-grade thermoplastic is highly versatile and commonly used in medical applications due to its durability, toughness, and strength, making it well-suited for making parts such as dental devices, implants, sutures, catheters, forceps, and clamps. |
PEEK | PEEK offers excellent tensile strength and can be used as a lightweight alternative to metal parts in extreme temperature and stress environments. It’s resistant to chemicals, wear, and moisture. |
Delrin (Acetal) | A resin with excellent moisture resistance, superior wear resistance, and low friction. |
PTFE (Teflon) | Teflon has superior chemical resistance and excellent performance in extreme temperatures compared to most plastics. It is highly resistant to solvents and is electrically insulated. |
Polycarbonate (PC) | PC has superior mechanical and structural properties with almost twice the tensile strength of ABS. Widely used in automotive, aerospace, medical, and other applications that require durability and stability, it is especially suited for solid infill parts that are fully dense. |
Polypropylene (PP) | PP is plastic with excellent electrical properties, low moisture absorption, the ability to carry light loads for extended periods in a variety of temperatures, and the capability to be machined into parts with chemical or corrosion resistance. |
UHMW PE | UHMWPE is a general-purpose material with high wear, chemical, corrosion resistance, and impact strength, low surface friction, and moisture absorption. |
Garolite G-10 | Garolite G-10, also known as epoxy-grade industrial laminate and phenolic, is a material composed of epoxy resin, reinforced with fiberglass fabric. It has high strength and low moisture absorption and can be CNC machined to be used as an alternative to metal components when magnetic features cannot be achieved. |
Factors to Consider When Selecting Materials for CNC Machining Medical Parts
When machining medical parts, it is essential to have a comprehensive understanding of the specific requirements and needs of the medical applications, as well as carefully consider a variety of factors. These are some key points to keep in mind:
On chemical resistance
Many medical products, such as diagnostic and testing equipment, surgical equipment, and ventilator masks & tubes, often require re-using, constant cleaning, and sterilization. Consequently, materials used for these components must have good chemical resistance.
Stainless steel is highly resistant to chemicals, and can withstand exposure to most organic compounds, acids, and bases. Similarly, titanium and aluminum are corrosion-resistant to certain chemicals. Plastic resins like PC and PEEK are also useful in this situation.
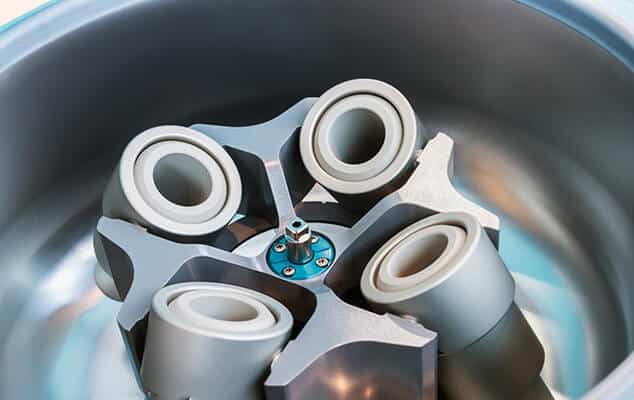
On radiation resistance
Medical parts may be exposed to radiation from sources such as magnetic resonance imaging, X-rays, and chemotherapy, and radiation will affect the service life of a product. It is therefore important to select machining materials that will not degrade when exposed to radiation, especially for equipment used in surgical operations, x-ray machines, and other diagnostic tools.
Titanium has low radiation absorption due to its high density. Additionally, resins such as PEEK, ABS, and PU are also good choices for these applications.
On biocompatibility
For long-term contact medical equipment, such as pacemakers, prosthetics, artificial heart valves, hearing aids, and artificial joints, strong and durable materials are essential. Biocompatibility is also a major consideration.
Titanium and stainless steel are two metals suitable for such requirements, as they are non-toxic and highly biocompatible with the body, allowing for safe contact with tissues. Moreover, plastic polymers such as Acrylic, PE, PU, and PET are also common materials in these applications.
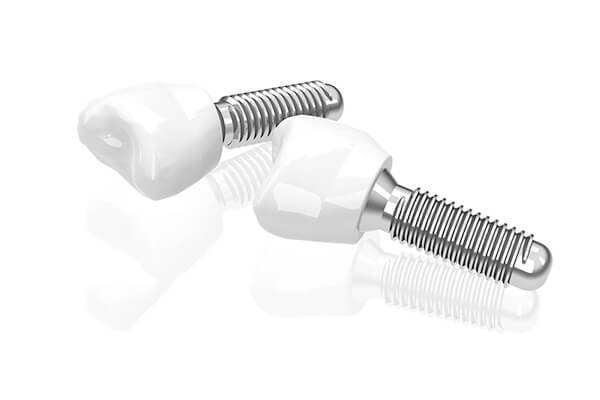
On the drug delivery system
When delivering drug dosages, it is vital to ensure aerosols and fine powders do not adhere to the surfaces of the material, as this could affect the accuracy of the dosage and subsequently the treatment outcomes. Therefore, there is a need to choose the right materials for cans, injectors, tubes, vials, and other drug delivery devices.
Stainless steel, aluminum, copper, and titanium all are metals with good static-dissipative properties, enabling them ideal for drug dispensers. Anti-static plastic polymers such as polypropylene, ABS, PC, and acrylic are also excellent choices.
On sterilization
In the medical industry, the common methods of sterilization are chemical vapor, steam, and radiation sterilization, which expose medical materials to degrading agents such as radiant energy, chemicals, and high temperatures. It is therefore essential to select materials that can resist these agents.
Stainless steel is a prevalent choice due to its corrosion resistance and ability to withstand repeated sterilization cycles and high temperatures. Titanium is also an excellent option due to its resistance to wear and corrosion from sterilization. Additionally, plastics like PEEK, PC, PU, and ABS are also available.
On prosthetics
When designing prosthetics, it’s vital to consider factors such as impact resistance, ease of forming, and strength. The required level of durability, location of the prosthetic, and its weight determine the material choices.
Titanium is commonly preferred due to its lightness, corrosion resistance, strength, and biocompatibility. Stainless steel and aluminum are also valuable metals, with aluminum being particularly suitable for lightweight applications. Plastic resins such as ABS+PC, PMMA, PEEK, glass-filled nylon, and High-Impact Polystyrene (HIPS) are also available for these applications.
On artificial joints
Plastics for artificial joints are determined by the individual patient’s needs and the specific joint being replaced. The materials used for semi-permanent or permanent joint replacements must be wear-resistant, strong, and biocompatible.
Titanium, stainless steel, and cobalt-chromium alloys are the most frequently used metals for artificial joints, due to their high strength, biocompatibility, and corrosion & wear resistance. Some of the most popular plastic resins used for these applications are UHMW, EEK, and PTFE.
How to Optimize Your Medical CNC Machining Projects
When it comes to producing numerous intricate medical components, CNC machining is an excellent choice. However, this process can be complex. To ensure optimal results from medical CNC machining, it is essential to follow the CNC machining design guide.
Design optimization
Part designs may be modified to enable CNC machining to perform in an easier and more efficient way. By simplifying the design of medical device parts during the CNC machining process, greater efficiency, lower costs, and higher precision can be achieved. This is typically done by:
- Part geometry can be simplified by eliminating extraneous features
- Utilizing standard features such as fillets, chamfers, and radii
- Material usage should be minimized
- The design should enable easy tool access
Simple maintenance
When designing CNC machined medical components, it is important to keep ease of maintenance in mind in order to ensure that the parts remain in proper and safe working order. A straightforward design easy to access can make maintenance tasks simpler and more effective.
Durable and easily cleanable materials can help increase the part’s lifespan. Additionally, to identify potential issues quickly and ensure timely maintenance and repairs, it’s recommended to incorporate monitoring systems into CNC machining medical devices.
Use bright colors
Coloring can be a useful tool for improving the identification and traceability of parts, especially those that are similar in size or shape. Bright colors can also help differentiate between different versions of a part, such as for functional testing or prototypes.
When deciding on colors for CNC machined medical parts, the specific requirements of the component and its intended use must be taken into account. For instance, some medical components require sterilization, and certain colors may be affected by harsh chemicals or high temperatures. What’s more, certain colors may degrade the biocompatibility of the part, so it’s vital to make sure that the color does not have a negative effect on the part’s function or biocompatibility.
Enhance aesthetically pleasing
Having an aesthetically pleasing design and vibrant colors can help a product stand out in a competitive market. These features create a positive customer impression and enable the product to be used or identified easily.
It is also essential to make sure that the design fits its intended uses and the specific requirements of the component. When selecting colors, emphasize the key features of the part, such as ports and buttons. Appropriate colors and textures should be chosen to improve the physical appearance of the part.
Improve portability
The optimization of the design of medical components for portability and convenience will enable easy transport and use in various clinical settings. This can be achieved by selecting lightweight materials such as aluminum, creating ergonomic designs, and designing components that can be easily detached. As a result, outcomes will be improved, versatility will be increased, and costs will be reduced.
Conclusion
CNC machining is an effective process to produce superior quality and highly accurate components for a range of medical applications. To meet medical application needs and strict requirements, design optimization, suitable materials, precision manufacturing process, and detailed inspection should be integrated to achieve the optimal result.
Your Reliable CNC Machining Expert in Medical CNC Machining – Dedasun Tech
In order to realize the best possible results, it’s of great significance to outsource a well-equipped and experienced CNC machine shop. Dedasun is an expert in CNC Machining and Sheet Metal Services who instantly provide pricing and on-time delivery for medical or dental projects, regardless of a one-off prototype or large-volume production. Our knowledgeable engineers and incredible manufacturing capabilities can assure you of a satisfactory outcome.
Dedasun is always ready to work with you to optimize your critical medical applications. High quality medical device parts that meet design specifications will be delivered in a timely manner. Email us your files today to get your project started!
Relevant News