12 Factors To Consider When Bending Sheet Metal Parts
Upload Time:
Sep 29, 2023
Bending sheet metal parts is a sequential which involves series of operations. In this article, you will learn some important factors for successful bending sheet metal parts. Let’s dive right in.
1. Tonnage
The maximum tonnage that a press can handle depends on a number of parameters. Some of these parameters are material properties and bend characteristics.
2. Length of The Bend
The measurement encompassing the point between the arcs of bend correspond to a metal part’s bend length. The tooling configuration of your equipment will influence its bend length.
3. Radius of the Bend
The bending process of a sheet metal part results in the extension of the outer part as opposed to the withdrawing of the inner section. The resulting rounded corner is the bend radius which varies depending on the material type and property, and tooling.
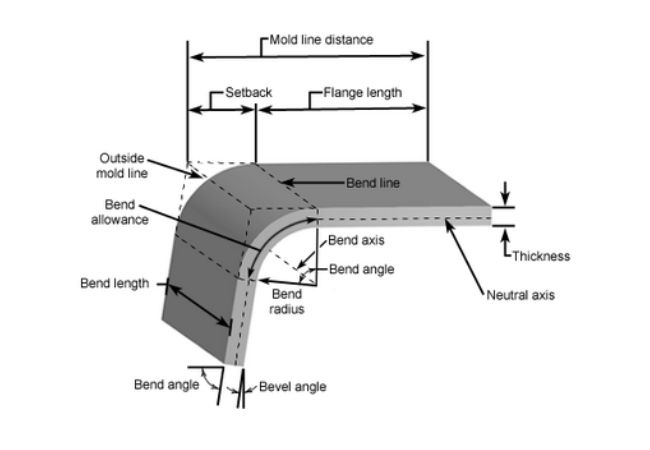
4. Bend Line In Sheet Metal
The location and geometry of the bends in your sheet metal parts are subject to bend lines. The bend line alongside bend angle and fixed geometry influence bend geometry characteristics. Bend lines are central for developing bend geometry and determining developed length.
In short, all these play an integral role in determining the sheet metal bending radius.
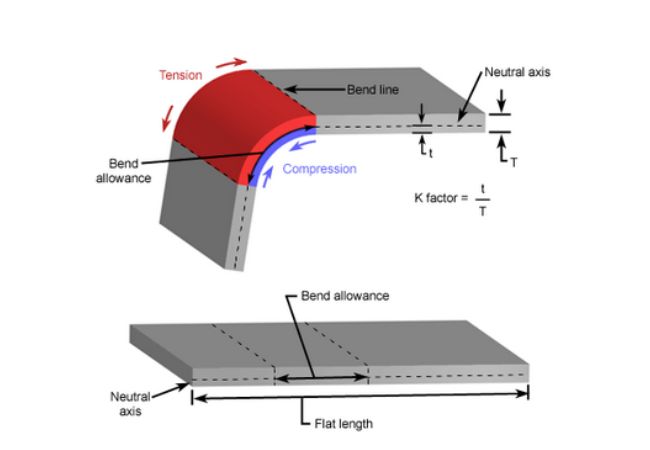
5. Hole to Edge Distance
Bending causes the material to stretch resulting in uniformly distributed internal stresses. These forces concentrate on the hole causing distortion when made in close proximity with the bend.
6. Distance between Bends
The tooling features of your equipment will determine how close your bends are upon bending. When producing bends, the tooling size and shape impose a physical constraint on bend closeness. Bends closely hurdled on similar sheet side impede tooling. Contrarily, bends on different sheet sides are unreachable thanks to base tooling’s breadth.
7. Heat Affected Zones
These result from heat procedures like plasma or laser cutting causing forming difficulties. These include uneven bending where there are holes and edges.
8. Bending Spring back
Springback causes the sheet metal part to bounce back after press application and removal. The sheet metal part tends to return to its former state thanks to the compressional forces exceeding tensile force.
As one of the key sheet metal bending rules, you should compensate for possible spring back.
Techniques such as coining can help compensate for bending spring back. However, this is only limited to certain materials such as thin stainless steel with thin gauge.
Choosing appropriate sheet metal bending machines such as modern CNC presses and air bending technique will help compensate for bending spring back.
Some of the most vital sheet metal bending calculation for spring back are:
Of course, Ks is the spring back factor. Additionally, you will calculate the initial bend angle and final bend angle.
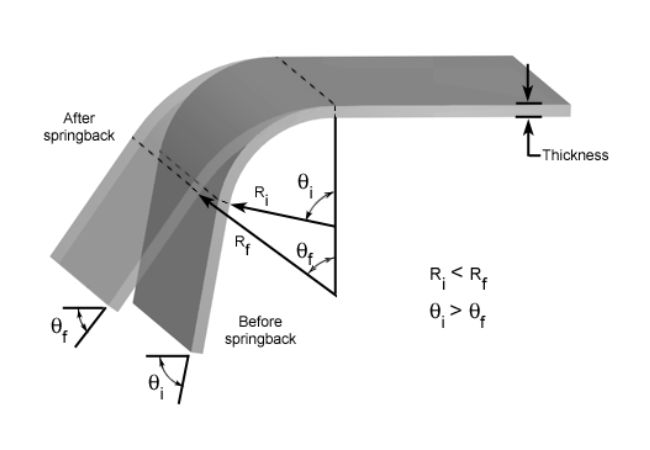
9. Sheet Metal Bending Tolerance
When bending sheet metal parts, the machine type determine the metal bending tolerance. It is difficult to achieve an exactly perpendicular corner while every corner will possess radius. Employ a standard tolerance for the bend angles at ± 1° and bend length at ± 0.010″.
10. Pressing Tolerance
During the bending process, you observe differences with sheet metal parts owing to material and aspects such as sheet depth.
11. K-factor and Bend Allowance
Sheet metal part aspects such as material composition and tooling settings influence the metal part’s K-factor. The mathematical representation of the k-factor is the material thickness to neutral axis ratio.
The lateral tangential distance of a bent sheet metal part taken along the axis of neutrality is the bend allowance. Usually, the neutral axis length remains unchanged post bending.
The formula for K factor is as follows:
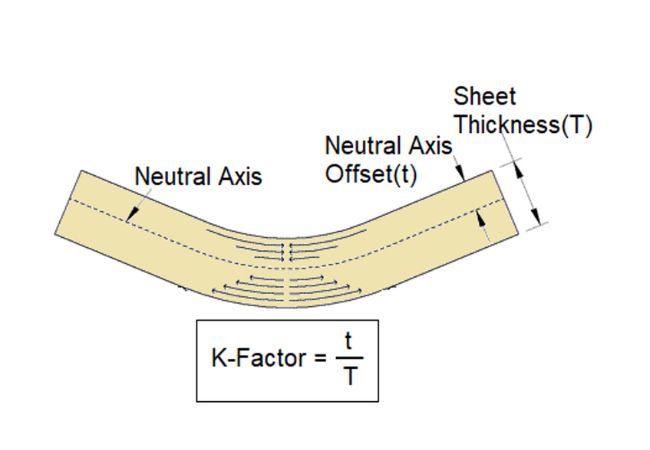
12. Bend Deduction
The overall sheet metal length after bending exceeds that of the originally flat sheet metal pattern. To get the precise flat pattern, you deduct a material length known as bending deduction from the sheet metal’s overall length.
Conclusion
Once you factor in all the 12 variable, you will definitely have high quality bent sheet metal parts. Of course, bending sheet metal parts will also require an understanding sheet metal and choosing suitable machine.
Relevant News