The Ultimate Guide to Metal Finishing
Upload Time:
Feb 24, 2024
Before choosing any metal finishing, you need the right information. This guide discusses some of the top 11 finishing operations for metal fabrication. So, before choosing any of the available options, read this guide.
Metal finishing is the act of applying a coating over a sheet metal’s surface. Sheet metal finishing encompasses activities such as cleaning or polishing of the surface before coating for the following reasons:
- Acting as priming coat for paint adhesion
- Creating an electrically conductive surface
- Enhancing resistance to wear
- Improving solderability
- Increasing part’s aesthetic appeal
- Increasing resistance to chemicals
- Limiting corrosion effects.
- Minimizing friction impact on sheet metal surface.
- Polishing, cleaning, and eliminating surface flaws
Surface Preparation for Metal Finishing
Surfaces preparation for metal finishing involves the removal of excess material to enhance post-finishing appearance. Common methods for surface preparation are:
- Metal Grinding: Employs different equipment called grinders to smoothen a part’s surface through friction.
- Metal Polishing: Involves buffing part surface into an even state by employing a polishing machine or cloth wheel.
- Sand Blasting: Employs abrasives such as sand or metal particles to smoothen the part surface by employing high speed shots.
- Tumbling and Rumbling: Removes burrs while smoothening edges by vigorously subjecting part in a drum with abrasive shots.
Metal Finishing Process
There are several finishing processes you employ for metal as follows:
1. Bead Blasting
In this technique, you use pressurized air to concentrate a flash of abrasive shards onto the substrate’s surface. This finishing method can also help eliminate paint strains on finished pieces.
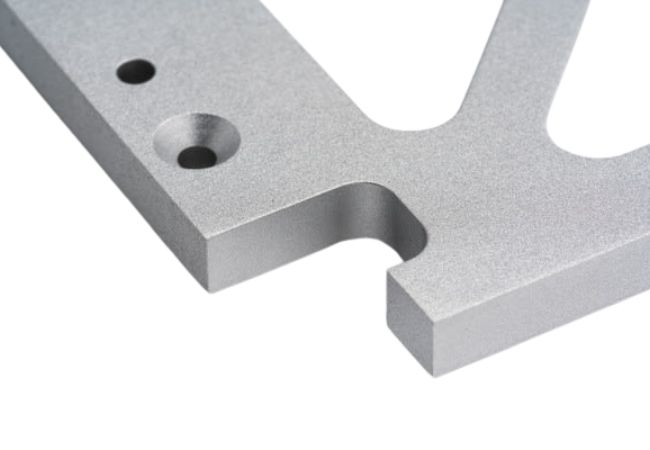
Advantages
- In comparison to other finishes, bead blasting is durable.
- Excellent for treating delicate surfaces.
- Sand or glass abrasives used in bead blasting are non-reactive.
- The procedure is safe with regard to the environment.
Disadvantages
- It is a time intensive sheet metal finishing process.
- It is not cost-effective for modest projects.
- Where you employ to silica as abrasives, it poses a health hazard.
- Requires extreme caution on application.
Application
- Finds use in applications with components requiring aesthetic quality given their impressive matte finish.
- Bead blasting also allows applications where you need additional finishing procedures.
Best Metals Suitable for Bead Blasting
- Steel, Aluminum, Brass, Stainless Steel
2. Anodizing
Anodizing coats the sheet metal via an electrochemical procedure such that it is resistant to corrosion. Here, you run an electric current through the sheet metal component immersed in a bath full of acid electrolytes.
When these elements combine, the surface of the metal part transforms into an integrated layer of anodic oxide. There are three versions of anodizing process as follows:
- Type I Anodization: Employs the application of chromic acid to the metal surface to produce a finish with thin layer.
- Type II Anodization: Employs sulfuric acid in place of chromic acid to create a robust layer that is resistant to corrosion.
- Type III Hard-coat Anodization: Also employs sulfuric acid and produces finishes with thicker coatings and high resistance to wear and corrosion.
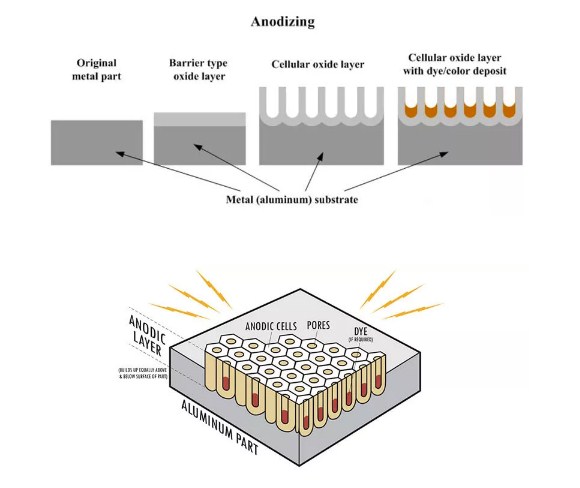
Advantages
- Chance of adhesion failure or fading is low.
- Easily affordable and environmentally friendly.
- Forms a coating that is an excellent electrical insulator.
- It has outstanding resistance to corrosion and abrasion.
- Results in flawless and permanent finish for sheet metals.
- The resulting coat is thinner than when using paint or powder.
- UV stability of the finished product.
Disadvantages
- Only compatible with aluminum and titanium.
- Low heat conductivity of metal finish.
- Delivers inconsistent results when using multiple metal sheets.
Application
- Type I anodization finds use in aerospace applications thanks to the thin and highly corrosion-resistant coating.
- The thin oxide layer produced in Type II Anodization subject to dyeing finds vast cosmetic application.
- Creation of automotive, mechanical parts and aviation parts, and precision instruments.
Best Metals Suitable for Anodizing
- Aluminum, Titanium
3. Powder Coating
Coats workpieces with dry powder producing a surface that is more durable and hard-wearing than regular paint. Powder coating can maintain the liquid suspension of the filler and binder without liquefying in contrast to traditional liquid paint.
Powder coatings achieve coatings of solid formations with larger depths unlike coatings formed by liquids. Since they involve no solvents, powder coatings are environment friendly as they release no volatile organic compounds (VOC).
You can perform powder coating by employing the following methods:
- Electrostatic Fluidized Bed Process: While similar to standard fluidized bed dip technique, here, the bed’s depth of powder is shallower.
- Electrostatic Spray Guns: Designates positive and negative charges to the coating surface and powder much like in electric charge theory. Usually, the surface bears negative charges and the paint positive charges.
- Electrostatic Magnetic Brush (EMB): Employs a roller in powder application coating producing reasonably fast application speeds and precise thickness.
Advantages
- It has outstanding resistance to corrosion and abrasion.
- Occurrence of adhesion failure, chalking or fading is low.
- Provides a huge selection of finishes for practically every metal material.
- The finished product is inflammable and non-hazardous.
- The resulting sheet metal coatings is durable.
Disadvantages
- When compared to conventional liquid coating, it costs more.
- You can't blend powders to get other colors.
Application
- Finds use in applying finishes to automotive parts such as side panels, fenders and hoods.
Best Metals Suitable
- Cold Rolled and Hot Rolled Steel, Spring and Stainless Steel, Galvanized Steel, Aluminium,
4. Electroplating
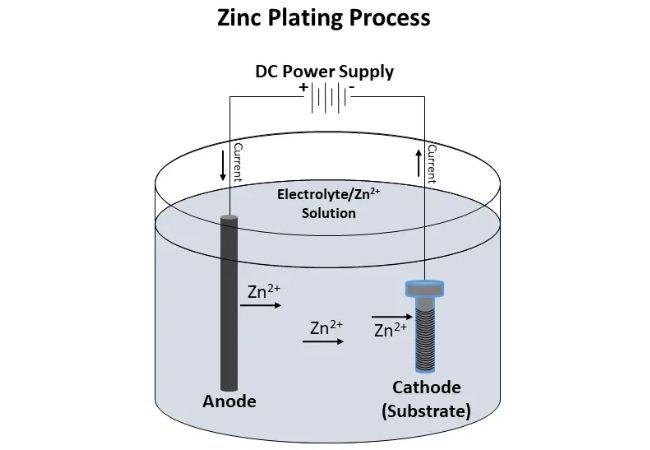
In electroplating, you electrically lay a metal plate over your sheet metal surface. You subject a liquid bath containing the dissolved metal ions to an electric current in this process.
You can electroplate the following metals to your sheet metal: Copper, Nickel, Gold, Brass, Iron, Zinc, Silver and Titanium. Before conducting electroplating, you perform a pretreatment procedure entailing washing, rinsing, and stripping.
Advantages
- Betters the sheet metal’s conductivity.
- It resists corrosion and abrasion quite well.
- It works with a variety of sheet metal materials.
- Minimizes occurrence of friction.
Disadvantages
- Application cost is high.
Application
- Useful in applications where you desire ornamental value as in gold-plated jewelry and parts.
Best Metals Suitable
- Aluminium, Copper, Steel, Titanium, Brass
5. Electrophoretic Coating
In E-coating, you envelop a metal substrate with a coating of epoxy in a very thin profile by using an electric current. You subject the piece in a bath containing desired coating material before employing an electrical current to stimulate the particles.
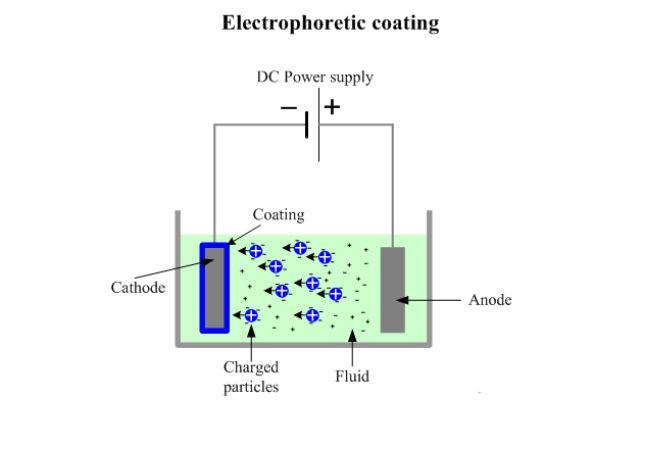
Advantages
- Provides resistance to corrosion.
- Offers thicker sheet metal coatings.
- Results in constant thickness with an even surface.
- Applicable in components with complex shapes.
Disadvantages
- Not applicable where cosmetic or visual appeal is desirable.
- Is not applicable with aluminium and stainless steel.
Application
- Finds application in automotive parts, hardware fixtures, agricultural parts, appliances, marine parts, furniture, tools and equipment. This is especially true when exposed to the elements in the outdoors.
Best Metals Suitable
- Aluminium, Copper, Steel, Titanium, Brass
6. Dacromet
This coating type utilizes a combination of binder with aluminium and zinc chips for spray applications or cold-dipping and finally heating.
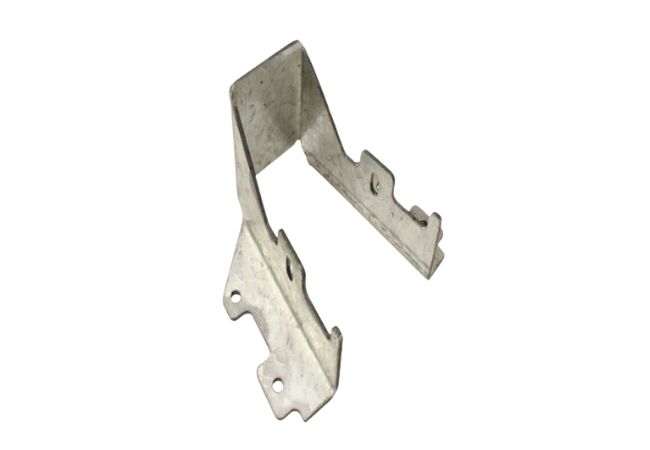
Advantages
- Improves corrosion resistance
- Highly reliable when it comes to resistance to chemical and mechanical damage.
- Offers effective surface protection despite the thin layer.
- The resulting finish can conduct electrical charge.
- You can paint over the finish.
Disadvantages
- Some Dacromet types may alter the mechanical properties of the metal.
- Is not a simple process.
Application
- Automotive, maritime and aerospace components, agriculture and construction, wind turbines and fasteners feature the dacromet finishing.
Best Metals Suitable
- Cold Rolled Steel, Hot Rolled Steel, Spring Steel
7. Passivation
Passivation employs chemical means to rehabilitate the substrate surface fortifying it from deterioration caused by corrosion posed by environmental elements. It is a capable treatment process before undertaking another plating procedure.
When performing passivation, you develop an oxide layer with a depth such that it staves off corrosion
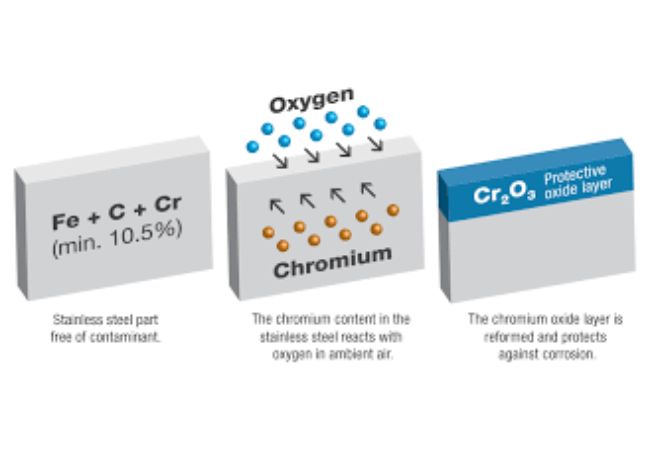
Advantages
- It does not change the sheet metal’s appearance.
- Enhances resistance to corrosion.
- Stainless steel descaling and cleaning processes are available.
Disadvantage
- Metal needs thoroughly cleaning before passivation or the operation may fail.
- Corrosion can develop from surface damage.
- Could require reapplication over the sheet metal part’s lifetime
Application
- Favorable as a secondary procedure to grinding, welding and cutting processes which modify the metal’s surface by bringing in foreign material.
- Making equipment for processing food and pharmaceuticals.
Best Metals Suitable
- Stainless Steel
8. Coating Using Chemical Film
Coating using chemical film is a sealant coating executable in the following categories:
- Type 1: Produces a golden brown finish employing the regulated substance hexavalent chromium.
- Type 2: Produces a transparent layer using trivalent chromium, zirconium, or titanium.
- Class 1A: Offers thicker coatings than Class 3 and enhances the base material’s resistance to corrosion while serving as a paints primer.
- Class 3: Offer improved resistance to corrosion without sacrificing electrical transfer capability.
Advantages
- Improve paint and powder coating adhesion to the sheet metal substrate.
- Preserve electrical transfer capability.
- Provides resistance to corrosion
- You can cover chemical film coatings with anodized finishes.
Disadvantages
- Save for corrosion resistance, they don’t provide any further resistance to wear.
Application
- Makes the industry coating standard in aerospace and military applications.
Best Metals Suitable
- Stainless Steel, Aluminium
9. Plating Electrolessly
Rather than employ electrical energy, electroless plating employs chemical means to deposit a metal sheet over the material surface. Uses a chemical bath with reducing capabilities to initiate a catalytic reaction that results in metal ions plating the sheet metal. You can plate using gold, nickel, copper and silver.
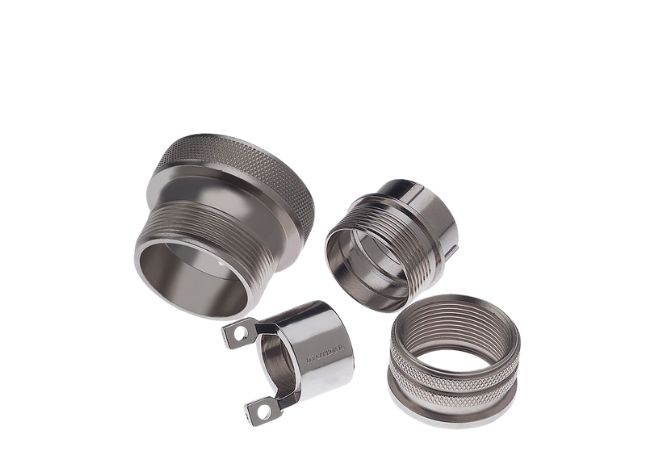
Advantages
- Makes a sheet metal tough.
- Provides resistance to friction and corrosion.
- Creates an aesthetically pleasing surface.
- Forms a uniform and even coat making it suitable for intricately shaped components.
- Heating can augment its mechanical qualities.
- Does not require electrical power or sophisticated equipment.
Disadvantages
- The component needs to be clean before plating otherwise it becomes vulnerable to damage.
Application
- Where you have sheet metal parts with intricate designs and desire an even surface.
- Where the sheet metal is vulnerable to corrosion stemming from environment of use.
Best Metals Suitable
- Stainless Steel, Aluminum, Copper, Brass
10. Spraying
You air-spray sheet metal with coating, typically varnish, paint or ink, using a spraying apparatus powered by compressed air. The two primary tools utilized for sheet metal spraying are spray guns and airbrushes.
There are many spraying methods such as airless spray guns, high-volume low-pressure guns, and air atomized systems.
Advantages
- Available in handheld and automated functions.
- Can have detachable heads allowing formation of various patterns.
- Capable of covering complex designs with depressed sections.
- Form even coating over large areas.
- Provides high-quality finish.
Disadvantages
- Can be a slow process when using the high-volume low-pressure gun.
Application
- Spray guns work well for evenly coating large areas and can be handheld or automated with detachable heads for various patterns.
Best Metals Suitable
- Spring Steel, Aluminum, Brass
11. Hot Blackening
In this process, you fashion a thin dark layer of oxide to the metal substrate. Various caustic materials, cleaning agents and coolants are necessary necessitating large volume productions.
Advantages
- Strengthens the metal’s resistance to abrasion.
Disadvantage
- Is not available in different colours.
Application
- Production of matte black coating in military presentations, vehicle parts, and weaponry.
Best Metals Suitable
- Aluminum, Galvanized Steel
Coating with Phosphate
Phosphatization is a chemical process you apply to sheet metals to produce a thin cohesive coating with impressive resistance to corrosion. Phosphates of manganese, iron or zinc are common.
Advantages
- Boosts corrosion resistance.
- Offers high adherence.
- Extends the life of organic coatings
- Offers suitable lubricant base
Disadvantages
- Resistance to corrosion is not as formidable as other coating types.
Application
- Useful as finishing precursor for secondary coatings like powder coating.
Best Metals Suitable
- Steel, Cast Iron
Selecting Right Metal Finishing
When selecting a sheet metal finishing, you need to consider certain factors:
- Cost: Select a sheet metal finishing technique within your budget. While techniques such as anodizing are expensive, you should balance quality and cost to be distinctively outstanding.
- Layer Thickness: Sheet metal finishing techniques have different resultant thickness. For instance, you can achieve much thinner coatings with electroplating than with powder coating.
- The Material Type: Certain sheet metal finishing techniques are only compatible with specific materials. Additionally, hardness varies with the material thus requiring different treatment.
- Turnaround Time: Where you have a limited production window, you employ a sheet metal finishing option that is quick. However, do not compromise on quality at the expense of time.
Relevant News