Sheet Metal Fabrication-The Ultimate Guide for 2024
Upload Time:
Feb 24, 2024
Do you know the sheet metal fabrication industry may grow by 3.8 billion USD in 2024? You can benefit from this significant growth by adopting cost-effective, accurate and modern fabrication technologies. Additionally, you must choose a suitable material, focus on quality, application and costs, to mention a few.
Fabrication refers to various processes or techniques you will use to transform sheet metal into valuable structures or products.
For example:
You may cut, bend or weld sheet metal to make a structure. Alternatively, you can punch, bend and drill to make a different structure.
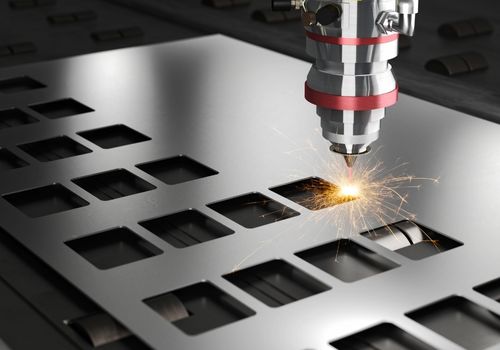
Chapter 2: Benefits Of Sheet Metal Fabrication
Nearly 97% of industries use sheet metal fabricated parts. It is due to the numerous benefits these parts offer.
However, you can only enjoy these benefits by choosing the correct fabrication technique, tool and material. You will learn more about this shortly.
Here is why you should choose fabricated metal parts:
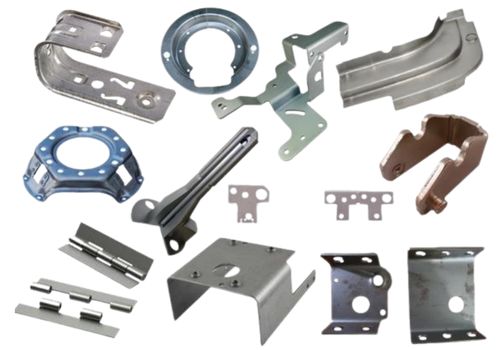
It is a Versatile and Adaptable Process
You can fabricate virtually all sheet metal types. Besides, you can make various part designs and shapes – from complex to simple sheet metal parts.
Easy to Control Cost
Cost is an essential parameter in any sheet metal fabrication process.
In metal fabrication, you can control virtually all parameters determining the overall project cost. For instance, you can choose an affordable sheet metal fabrication technique, material or surface finish.
You Can Produce a Range of Parts and Components
Whether you want simple or complex parts, fabricating sheet metals offer unlimited possibilities. Additionally, you can make small to large sheet metal parts.
Easy to Control Quality
Choosing the best metal fabrication technique, and working with a highly trained team, will guarantee quality parts.
Additionally, you can opt for a precision sheet metal fabrication process. Here, you will use CNC machines, which produce accurate parts.
You have Competitive Edge
Fabricating sheet metal will give you a competitive edge. You can control the quality, features and cost of the entire project.
It is Effective and Efficient
It is easier to optimize the fabricated sheet metal part designs. As a result, you increase efficiency.
Additionally, increasing production capacity will be an easy process.
In short, fabricating sheet metals offer many benefits in modern industries.
Chapter 3: Sheet Metal Fabrication Process
Fabricating sheet metal parts can be a simple or complex process. It will depend on the sheet metal part design.
However, the critical stages in the entire process remain the same.
Let’s take a look at some of the key processes:
Design Sheet Metal Part
Design is the first step in the sheet metal fabrication process. There are many CAD software that will help in the design process.
Whether you opt for in-house or outsourcing sheet metal parts fabrication, a good design will translate into better components.
Additionally, you must pay attention to the following:
- Design for manufacturability (DFM) will help you evaluate the viability and practicality of fabricating sheet metal parts.
- Sheet metal prototype fabrication – you will make a sample product for testing, quality verification and approval before mass production starts.
Cutting Sheet Metal
Sheet metals are available as coiled strips or flat pieces. Therefore, you will cut the section you need for subsequent processes.
You may also refer to cutting sheet metal as a subtractive fabrication.
You will choose the cutting technique depending on the sheet metal gauge, part design, material type or available resources.
Let’s look at the standard cutting techniques:
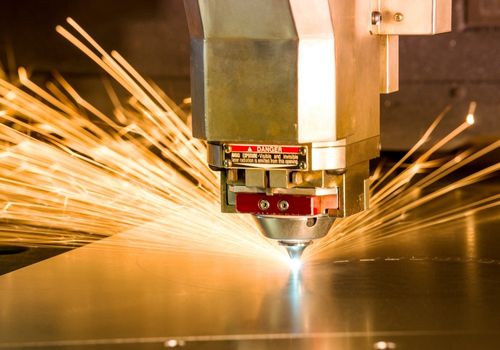
Laser cutting is suitable for precision sheet metal fabrication. The machine uses an intense laser beam to vaporize sheet metal parts – hence cutting accurate pieces.
Some notable aspects about laser cutting sheet metal are:
- High accuracy and energy efficiency
- Suitable for medium to thin sheet metal gauge
- Cutting or penetrating hard sheet metals can be a challenge
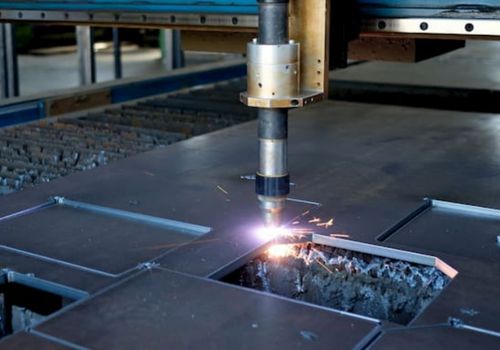
In a plasma cutter, an ionized gas cuts the sheet metal parts. Usually, the ionized gas has an extremely high temperature.
The material will melt by directing the gas stream on the sheet metal.
Ideally, the process involves the formation of an electric arc.
Even as you choose plasma cutting sheet metal, it is worth noting the following:
- The process is powerful
- The degree of accuracy is less than Waterjet cutting sheet metal or laser cutting sheet metal
- It can cut sheet metals with thick gauge
Waterjet Cutting Sheet Metal
A mixture of high-pressure water jet and abrasive materials cut the sheet metal. You can cut sheet metal into various shapes and sizes.
Waterjet cutting is a perfect option for sheet metals with low melting points.
Remember, Waterjet sheet metal cutting does not produce heat.
Cutting Sheet Metal With Saw
You can use a hack, circular, jigsaw, band, or table saw to cut sheet metal. Of course, these are the most common options for DIY projects.
This sheet metal cutting technique is suitable for small to large projects. You can handle simple to complex projects.
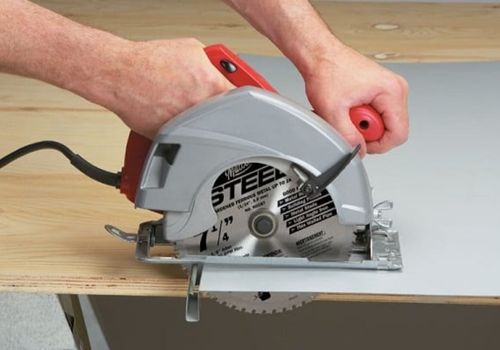
Although these are some of the most common techniques you will use to cut sheet metal materials. Others may include:
- Drilling sheet metal – You will remove sections of the materials by creating holes in sheet metal.
- Milling sheet metal – a rotating cutter will remove unwanted sheet metal parts.
- Grinding sheet metal – a grinder gradually removes unwanted sheet metal sections.
Additionally, you can use punching, piercing, perforating and blanking. They may also form part of sheet metal cutting processes.
After cutting the sheet metal, you can transform the section into different shapes and designs.
How can you achieve this?
Sheet Metal Deformation Or Forming Sheet Metal
Deformation or forming involves transforming the sheet metal into different shapes and designs. Again, there are various techniques you will use, such as:
Sheet Metal Bending Process
Sheet metal bending is the plastic deformation of a workpiece over a specific axis. As a result, it changes the sheet metal’s geometrical shape.
You may consider these options to bend sheet metal parts:
- V bending sheet metal
- Bottoming sheet metal
- Coining sheet metal
- Air-bending sheet metal
- Wipe bending sheet metal
- Roll bending sheet metal
- Rotary draw bending sheet metal
- Step-bending sheet metal
Closely related to sheet metal bending is sheet metal folding.
Whichever technique you choose, the final part will have unique shapes and properties. Therefore, you must understand how every process works.
By the end of this process, you will have unique sheet metal with a specific shape.
Apart from the bending process, other fabrication techniques you may use to deform sheet metals are:
- Spinning sheet metal will help you form axially symmetrical round metal parts. A lateral force transforms the material into a suitable shape as the workpiece rotates on the spindle.
- Hydroforming sheet metal – using a special die and pressure, you can deform sheet metal into different shapes.
- Embossing sheet metal creates raised or sunk parts on sheet metal surfaces. It is a popular marking technique.
At this point, you can have a finished sheet metal fabricated part. Otherwise, you should proceed to other processes such as:
- Sheet metal parts assembly
- Apply surface finish on sheet metal parts
You will learn more about these two shortly.
Chapter 4 Sheet Metal Assembly
A sheet metal part may have the following:
- A single unit/one piece
- Different parts joined together
If your part has more than one unit, sheet metal assembly is critical.
Sheet metal assembly involves joining different sections to form a whole part. Therefore, the type of sheet metal assembly technique will depend on:
- Type of joint you need – whether permanent or temporary
- Strength of the joint
- Type of material
- Sheet metal part design
- Sheet metal part application, amongst others.
Specifying the type of assembly technique during the design stage is essential.
Some of the most common sheet metal parts assembly techniques include:
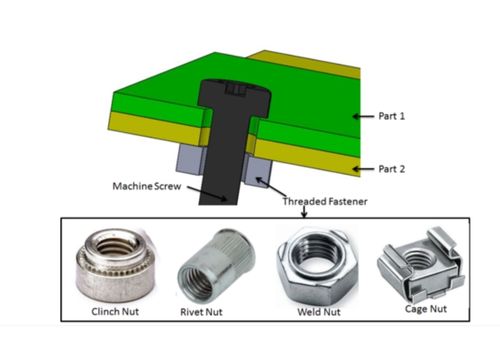
You can use bolts and nuts to assemble sheet metal parts. Alternatively, you can use screws.
You can quickly assemble and disassemble the fabricated sheet metal parts with fasteners.
Welding Sheet Metal Parts
Welding sheet metal parts are perfect for permanent and strong joints. Depending on the type of material, you can choose any of the following welding techniques:
- Fusion welding
- Arc welding – some of the most common options include gas metal arc welding, shielded metal arc welding, submerged arc welding, tungsten inert gas, electro-slag welding, flux cored arc welding, arc stud welding, electro-gas welding, atomic hydrogen welding and carbon arc welding
- Gas welding – available options are air-acetylene welding, oxy-acetylene welding, oxy-hydrogen welding and pressure gas welding
- Resistance welding – available options include resistance spot welding, resistance seam welding, projection welding, percussion welding, flash welding and upset welding
As you can see, there are many sheet metal welding techniques to choose from.
Closely related to welding are soldering and brazing. In these techniques, you will use metal filler to weld.
Riveting Sheet Metal Parts
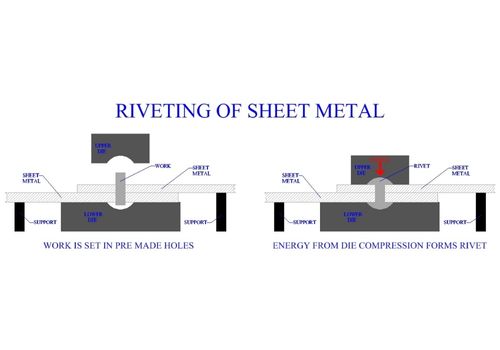
Riveting forms durable and robust joints. It is a perfect option for parts subjected to fluctuating temperature and pressure.
Some common designs are solid rivets, tubular rivets, self-piercing rivets, blind rivets, and flush rivets.
Apart from these sheet metal assembly techniques, others include;
- Tongue and groove sheet metal assembly
- Adhesive bonding sheet metal assembly
- Assembling sheet metal using hemming
- Snap fits assembly technique
- Using clinching and tabs to assemble sheet metal
Whichever process you choose, the final sheet metal part should be robust, durable and reliable.
Chapter 5 Surface Treatment for Sheet Metal Parts
After fabricating sheet metal parts, and the subsequent assembly process, it is time to apply surface treatments.
Typically, these surface treatments for sheet metal parts will:
- Improve aesthetic appeal
- Improve corrosion resistance and hardness
- Add extraordinary features on the sheet metal part
Depending on the sheet metal part and materials, you may consider many surface treatment options.
Let’s have a quick overview:
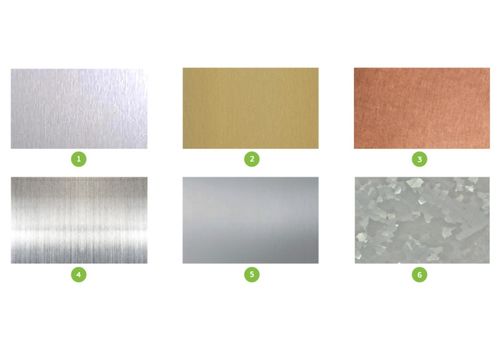
Electroplating Sheet Metal Parts
A thin metallic coating will form on the fabricated sheet metal part during electroplating.
It is one of the most common surface treatment options. In most cases, electroplated nickel and electro-galvanizing are the most common.
Electroless Plating
Unlike the electroplating process, this process does not require electricity.
Anodic Oxidation
It is a perfect choice for fabricating aluminum and titanium parts. Here, a thin film will form on fabricated sheet metal parts, thereby:
- Improving aesthetic appeal
- Preventing corrosion on metal surfaces
- Improving wear resistance
Hot Dipping
You will dip fabricated sheet metal parts in the desired metallic coating. These can be lead, tin, aluminium or zinc.
As a result, it forms a coating which is:
- Corrosion resistant
- Better aesthetic appeal
Chemical Treatment
Through a series of chemical reactions, chemical treatment will form a thin film on the fabricated sheet metal part. It is a popular process for:
- Sheet metal part coloring
- Priming sheet metal surface before painting
- Protecting surface from corrosion
Vacuum Plating
Some of the most common techniques which use this technology include:
- Ion plating and implantation
- Vacuum vapour deposition
- Sputtering
Thermal Spraying
In this technique, you will melt the coating material and apply it to the fabricated sheet metal components.
The surface treatment will protect the metal part against high temperature and friction.
Powder Coating
You will spray powder coating on sheet metal parts. The sheet metal will absorb the powder.
Next, you will bake the sheet metal part at a reasonable temperature for a powder to flow on the entire surface.
Painting
Whether you opt for wet or liquid painting, it makes the surface corrosions resistant and improves aesthetic value.
Additionally, you can use silkscreen printing, abrasive blasting or chromate coating.
As you can see, many surface treatments for sheet metal parts exist. Always talk to a professional sheet metal fabricator for advice on suitable surface treatment.
Chapter 6: Sheet Metal Fabrication Cost
Cost is a vital element in the sheet metal fabrication process. Every sheet metal fabricator strives to find affordable solutions.
Of course, a low-cost sheet metal fabrication does not imply low-quality parts.
With these in mind, let’s look at critical aspects of controlling sheet metal fabrication costs.
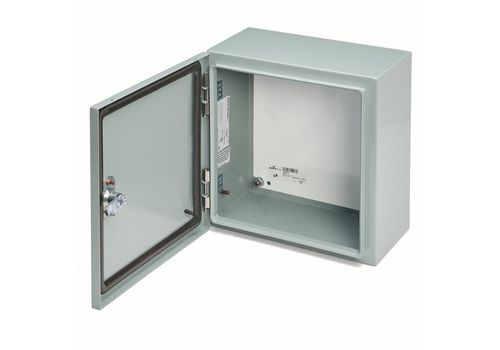
Factors Determining Cost of Sheet Metal Fabrication
Many factors determine sheet metal fabrication cost. They include:
Type of Material
First, the sheet metal types will determine how much to pay for the fabrication process. Ideally, the cost of stainless steel, aluminium, or copper varies.
Secondly, the sheet metal grade, gauge and size determine sheet metal fabrication cost estimation.
Sheet Metal Fabrication Technique
The fabrication technique will determine sheet metal fabrication cost. For instance, the cost of cutting sheet metal with a laser machine is different from a hand saw.
Of course, this also goes hand in hand with labor.
Nature Of Sheet Metal Parts
Complex parts are more challenging to fabricate than simple designs. It is because you will require sophisticated technology to fabricate the sheet metal parts.
Again, the degree of tolerance and accuracy will also determine the sheet metal fabrication prices.
Final Surface Finish and Assembly
The final finish on the sheet metal part will determine the overall cost during the fabrication process.
Of course, the same applies to the sheet metal assembly process.
Relevant News