The Ultimate Guide to Aluminum Sandblasting
Upload Time:
Feb 25, 2024
Before sandblasting aluminum, read this guide. It has all information that will help you understand every process, techniques and best material for sandblasting aluminum.
What Is Aluminum Sandblasting?
Aluminum sandblasting is the process of forcibly applying solid abrasive materials to an aluminum surface. Such abrasive materials includes sand and glass beads which smoothen or roughen the aluminum surface, remove paint, or change its surface features.
Sandblasting of aluminum is necessary for a variety of reasons:
- Taking off the primer or paint from the manufacturer.
- Clean off mold or rust.
- As pretreatment for a new coat of paint or powder coating.
- Removal of aged or damaged and addition of decorative elements.
- Cleaning up after damage caused by fire.
- Smoothing a rough aluminum surface.
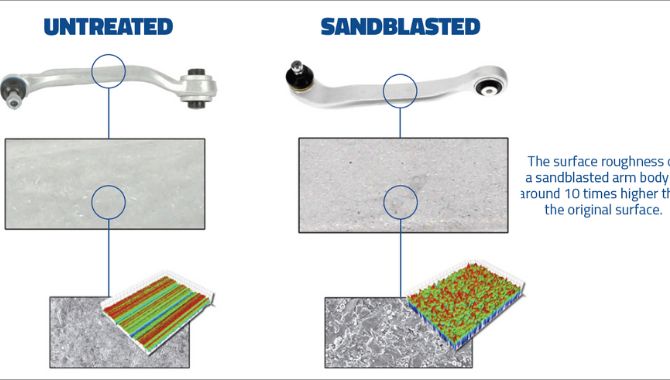
Key Abrasive Properties of Media for Sandblasting Aluminum
The following constitute the key abrasive properties of media used in abrasive blasting of aluminum: size, shape, hardness and density.
Shape
Round particles are less abrasive than coarse ones. The depth profile in sandblasting aluminum depends on the abrasive particle angle sharpness. An abrasive particle that is sharp penetrates aluminum surfaces more deeply.
The four major shapes of abrasive media are:
- Round such as silica sand and smooth glass beads.
- Sub-roundedg. staurolite and walnut shells.
- Angular which is the sharpest such as coal slag and crushed glass.
- Sub-angular like olivine, garnet, and plastic.
Size
You gauge a particle’s size based on the size of the mesh it can pass through. A mesh size of 300 would imply very small particles, whereas a mesh size of 10 would suit comparatively large particles.
Larger particles have greater momentum and consequently produce impact craters that are larger. However, these particles have more focused effects on the metal surface.
Therefore, best way to achieve a consistent depth profile and finish is to employ the smallest abrasive particles. This allows you to achieve the necessary anchor pattern.
Hardness
The harder an abrasive particle is the further it penetrates the aluminum surface during sandblasting. A soft abrasive has a reduced or nonexistent anchor pattern finding use in cleaning procedures that eliminate grease, dirt, or paint.
Very hard abrasives are brittle and subject to fracture upon making contact with the metal surface. Some of the particle’s kinetic energy dissipates during breakage reducing influence on surface transformation.
Density
A particle’s density describes a particle’s behavior when it collides. You find dense particles possess higher mass to volume ratio.
Consequently, a denser particle achieves a larger depth profile given it exerts a larger pressure on impact. You observe this to better that made by a corresponding mass but larger particle.
Furthermore, denser particles exert higher kinetic energy during impact unlike less dense particles which collapse absorbing some of the energy. You can still employ such particles in minor cleaning operations and paint removal.
Types of Aluminum Sandblasting Media
Some of the media you employ include:
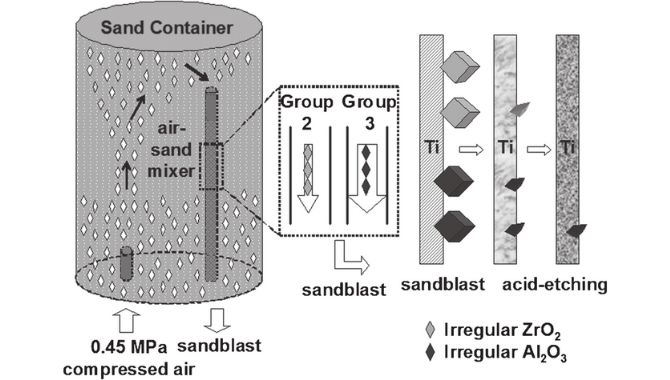
Crushed Glass
Typically consists recycled glass finding use in coating removal and identified by the sharpness of its profile. The result in employing this finish is clearer compared to sand and slags.
Notable features include:
- Hardness between 5.5-7 Mohs.
- Density of 2.5 SG.
- Angular Shape
- Non-toxic as it eliminates harmful airborne particles.
- Fast and can work with water.
- Depth pattern between 2 – 6 mils.
- Pressure requirement between 80 – 150 psi.
- Non-recyclable.
Aluminum Oxide
Aluminum oxide is a hard abrasive that is affordable finding use in paint removal, deburring and etching. It is available in different sizes with the capacity to smoothen out edges in polishing procedures.
Notable features include:
- A hardness of about 9 Mohs.
- Angular particle shape.
- Depth profile between 1 mil to 16 mils.
- Fast process employing 60 psi to 100 psi in impact.
- Supports reuse up to eight cycles.
Staurolite
Staurolite is essentially a silicate derivation of iron and silica extracted from metamorphic rocks. It is an effective abrasive for removing thin coatings of pain, rust and milling scales.
Other notable features are:
- Little dust production compared to other abrasives.
- Has a sub-angular shape useful in reduced surface profiling.
- Hardness of 7.0 Mohs.
Plastics
Plastic abrasives find varied uses in sandblasting aluminum given their availability featuring different key properties. Polycarbonates and polystyrene are some of the major compounds in plastic abrasives useful in paint and mold removal from delicate surfaces.
Key features include:
- Leaves no anchor pattern thanks to being soft and light.
- Less-hazardous compared to chemical stripping.
- Fast abrasive material.
- Hardness between 3-4 Mohs.
- Density of 1.5 SG.
- Angular
Walnut Shells
Black walnut shells are a great abrasive material suitable for sensitive applications like polishing and cleaning operations. This is because walnut shells are natural organics and less rigid than similarly employed plastics and metals.
Walnut shells are useful for polishing jewelry, cleaning motors and airplane engines, repairing antique surfaces and cleaning dies and molds. Some of its prominent features are:
- Don’t cause anchor patterns.
- Mesh size between 6 – 100.
- Hardness ranging between 3 – 4 Mohs,
- Density range: 2 – 1.35 SG.
- Sub angular
- Slow sandblasting process.
- Pressure requirement of 60 psi to 100 psi.
- Single use and non-recyclable.
Corn Cobs
Corn cobs are a soft, natural abrasive made by grinding corn cobs useful in delicate sandblasting. This abrasive material removes dirt, grease and coatings while mostly preserving the aluminum surface.
You can also employ it for deburring and polishing with the following features:
- It is non-toxic making it safe for operators.
- Has angular shape.
- Its hardness ranges about 4.5 Mohs.
- It is a slow procedure employing pressure between 60 psi to 150 psi.
- Can usefully work in a single cycle.
Silica Sand
While formerly the most common sandblasting medium, its limited use currently stems from its toxic nature. The silica content causes respiratory issues when inhaled. Furthermore, the moisture presence in sand remains in the equipment hastening aging.
However, its primary features are:
- Mesh sizes of 6-270.
- A hardness between 5-6 Mohs
- Density: 65 SG
- Round shape.
- Low cost.
Garnet
It is a naturally occurring mineral deposit of silicate derivation with exceptional abrasive qualities. It has good coating preparation and adhesion qualities finding use in both wet and dry sandblasting.
It is a reliable all-purpose abrasive for outdoor surface preparation whose removal of tough coatings, rust and paint is exceptional. Other outstanding features include:
- It has a high stripping rate,
- Produces little low-dust
- Has low consumption.
- Allows close feathering control.
- Mesh size is between 30-120 with density at 5-4.3 SG
- Hardness ranges between 7-7.5 Mohs
- Has sub-angular
- Is a fast method employing pressures between 60 psi to 120 psi.
- Supports a low cycle count not in excess of four cycles.
Glass Beads
These preformed spherical medium result in exceedingly smooth and brighter surfaces compared to angular abrasives. Glass beads find use in polishing aluminum, propellers and turbine blades.
They also serve general cleaning purposes, peening, making cosmetic finishes, removing automotive paint and other surface contaminant. Its major highlights include:
- Ability for recycling reducing running costs.
- Mesh sizes of 30-325
- Hardness of 5-6 Mohs
- Density of 5 SG
- They are rounded.
- Require application pressure between 40 psi to 80 psi.
Soda
Bicarbonate of soda is the source of soda abrasive which is non-damaging especially when used for cleaning and removal of paint. It can also remove rust from metal surfaces without causing deformation with the following features:
- Has angular shaped particles.
- Has a hardness of 2.5 Mohs.
- Employs pressure between 50 and 150 psi.
- Is a non-recyclable medium.
Considerations When Selecting Blast Media for Aluminum
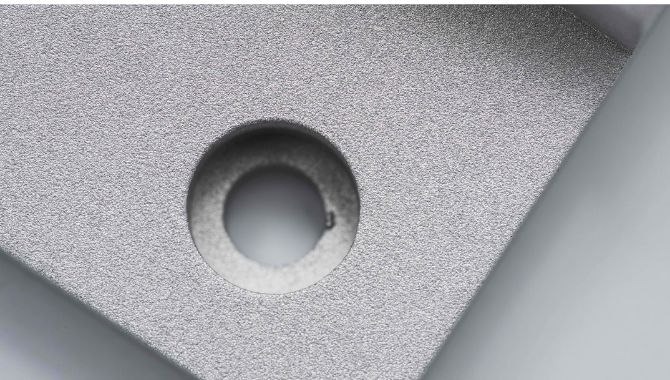
The most used abrasive media for aluminum surface blasting are glass beads, sodium bicarbonate, or walnut shells. The following guidelines for basic sandblasting best practices explain how to pick the appropriate media for your goals:
Abrasive Properties
A sharply edged abrasive quickly cuts through the surface under treatment. Deeply pitted surfaces pose a problem where the abrasive material is too soft.
Steel Grit/Steel Shot
Avoid using steel grit or steel shot on aluminum surface sandblasting. Steel harness exceeds that of aluminum and can produce surface profiles that encourage corrosion.
Crushed Glass/Aluminum Oxide
Crushed glass and aluminum oxide are reliable options when working on aluminum for repainting or powder coating. Aluminum oxide’s anchor profile thanks to its toughness, angular structure and reusability, makes the new coating’s adhesion easier.
Glass Beads
Employ glass beads where you want a polished appearance on your aluminum surface. They are excellent finishers that leave surfaces clean and crisp and are also reusable.
Fine Abrasive
Employ the finest sandblasting medium that helps achieve the desired surface preparation characteristics. You will get more impacts per volume using a fine abrasive.
Thin Aluminum Surface
For thin aluminum surfaces, commence with low pressure of about 55 psi before gradually raising to prevent warping. When using a blast cabinet, its size and nozzle influence the pressure parameter with a direct correlation.
Pre-Test
Start by testing a small section of the aluminum surface under treatment. Continue upon confirming the outcome to be acceptable.
Size and Shape of Substrate
The aluminum product’s size and shape influences the choice of the abrasive medium’s shape, hardness, and size. The efficiency of the abrasive, resultant surface finish, and cost-effectiveness depend on the key parameters.
Wet and Dry Abrasive
When considering wet and dry abrasives keep in mind the former has reduced velocity and efficiency than the latter. Consequently, you eliminate less product and employ reduced media. Furthermore, the nozzle assembly’s lifespan reduces under wet conditions thanks to the high pressure requirement.
Application of Aluminum Sandblasting
There are several uses for abrasive blasting of aluminum including the following:
- Removal of paint on automotive and marine vehicles during restoration.
- Cleaning aluminum surfaces by removing molds such as in boat hulls.
- Surface profiling for improved adhesion of coatings.
- Eliminating heat treatment.
Equipment for Sandblasting Aluminum
Here are some essential pieces of equipment to improve your sandblasting results:
Sandblaster
The sandblaster is an effective, portable, and simple device that generates a strong flow of abrasives to eliminate surface contaminants. It is ideal in cleaning aluminum substrates where conventional approaches fail.
Mechanism for Propulsion
The flow of abrasive medium is thanks to a mechanism for propulsion usually an air compressor. The compressor pressurizes air which expels the abrasive medium at designated pressure.
Nozzles
The abrasive stream’s flow and direction are under the direction of the nozzle that is available in a variety of sizes and forms. Ensuring the blast nozzle’s tip keeps a high rotation is necessary to propel the abrasive media.
Blasting Pot
This equipment is resistant to pressure and contains the pressurized air and abrasive media. Its size varies with the abrasive media type and quantity.
Blast Cabinet
You perform sandblasting under high pressure in a blast cabinet employing specially designed gloves fabricated with it. This cabinet encloses the aluminum substrate shielding you from the resultant dust and abrasive particles that it collects allowing recycling.
Blast Room
While similar in use to the blast cabinet, the blast room handles larger objects under treatment such as motor vehicles and aircrafts. Treatment in this room is dependent on the objects requirements.
Blast Guns
These guns do not require cabinets or pots finding common use especially for custom aluminum abrasive sandblasting operations. It functions similarly to blast pots with the abrasive media leaving via the housing.
Safety Tips While Sandblasting Aluminum
Some of the fundamental safety guidelines when undertaking abrasive blasting of aluminum are:
Electrical Equipment Dangers
Keep electrical equipment away from an active sandblasting site to about 50 feet while ensuring presence of safe grounding. When conducting abrasion of aluminum indoors, switch off and disconnect all electrical connections to prevent unintended connections.
Gases and Vapors can be Dangerous
When undertaking sandblasting of aluminum, production of hazardous vapors and gases is imminent. For instance, fly ash and silica dust can instigate major respiratory difficulties.
Personal Protection Equipment
When sandblasting aluminum, wear personal protective equipment such as an air-purifying respirator, blast helmet, overalls, gloves and safety boots. This ensures you are shielded from the fast moving abrasive particles and any produced fumes.
Advantages of Aluminum Sandblasting
Among the benefits you experience in employing sandblasting aluminum are:
i. A smooth surface with no infractions in hard to reach areas.
ii. Employs less equipment with only concern being personal protection.
iii. It is an expedient procedure that saves you time.
iv. Provides excellent surface preparation for secondary procedures.
v. Results in an aesthetically appealing aluminum surface with a shine or matte finish.
vi. You get a clean surface free from contaminants such as dirt and grease.
Disadvantages of Aluminum Sandblasting
Some of the drawbacks you experience are:
i. While it employs low equipment, the equipment such as blast containers and pots are quite pricey given the type and scale of use.
ii. Employing sandblasting for aluminum treatment poses health risk especially when using silica sand which produces toxic fumes.
iii. You require adequate space which may be expensive or unavailable when sandblasting aluminum given the ventilation needs.
Can you sandblast aluminum?
If your aluminum parts need the sandblasting process, we’ll make quality sandblasting surface. KDMfab has in-house sandblasting department, and this will make your order schedule at the right time. We also provide sandblasting service based on your requirement, whether the material is aluminum or other metal, products like wheels, bike frame, fence, die casting parts, or injection parts, we can always provide you with the best sandblasting solution.
Conclusion
With the information above, certainly you can easily sandblast aluminum material.
Remember, you can also use the same techniques to sandblast other materials.
If you have any questions about sandblasting aluminum, feel free to contact us.
Relevant News