Brass Finishing – The Ultimate Guide
Upload Time:
Feb 25, 2024
Any brass part manufacturing process is not complete without applying suitable surface finish. It doesn’t matter whether you are fabricating brass or casting brass, you will apply a surface finishing. In this guide, you will find all information about brass surface finishing and techniques. Whether you want to learn about electroplating, satin brass, or antique brass finishing, you will find all information right here.Brass finishing allows you to protect your brass surface by enhancing its resistance to corrosion, wear and touch. You can make a brass finishing choice depending on your needs and budget.
Importance of Applying Brass Finishing Operation
Brass finishing involves the treatment of the surface to assume certain qualities. You can achieve this by adopting various finishing operations.
Ideally, these surface finishes on brass parts aim to achieve different functions such as:
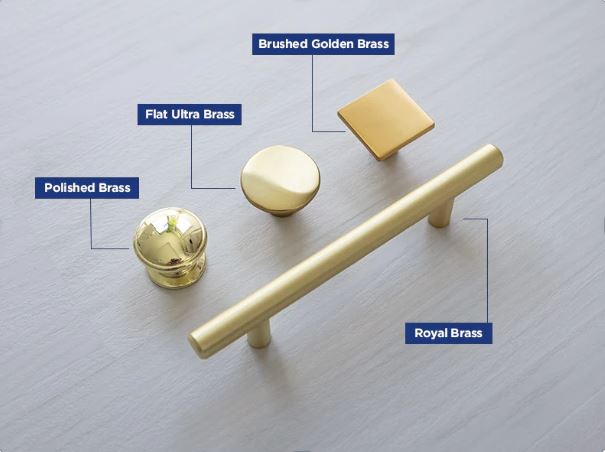
1. Eliminates Surface Defects
After processing brass parts or products, the surface may feature surface defects like scratches, nodes and burrs. A brass finishing operation eliminates these surface defects allowing you to achieve a uniform and consistent surface.
2. Improved Appearance
Using finishing operations on brass such as polishing can leave the surface smooth and shining. As result, augmenting its appearance.
Improving the appearance of brass products is especially useful when processing ornamental pieces or instruments.
3. Less Cleaning Difficulties
Finished brass typically has a smooth surface.
Normally, the smooth surfaces reduces the ability of contaminants to adhere to the surface. Consequently, this simplifies the cleaning of brass surfaces by eliminating the need of cleaning chemicals and making short work of it.
4. Improved Resistance
Applying a finishing operation on brass is essential in enhancing its surface resistance to corrosion or wear from chemicals or elements. This improves the durability of the brass surface thus extending its longevity.
5. Enhance Paint Cohesion
Undertaking a brass finishing operation can also be useful as a secondary process before painting. Polishing a brass surface for instance can act as primer to increase the adhesion of paint pigment to the brass surface.
Types of Brass Finishing Options
There are several options for brass finishing that you can employ in your project. Some common options include:
Electroplating Brass
In electroplating, you utilize electric current to initiate deposition of a thin metal coat over brass such as chrome or nickel. Electroplating improves the brass surface’s resistance to corrosion and wear.
At the same time, it is also capable of enhancing surface appearance.
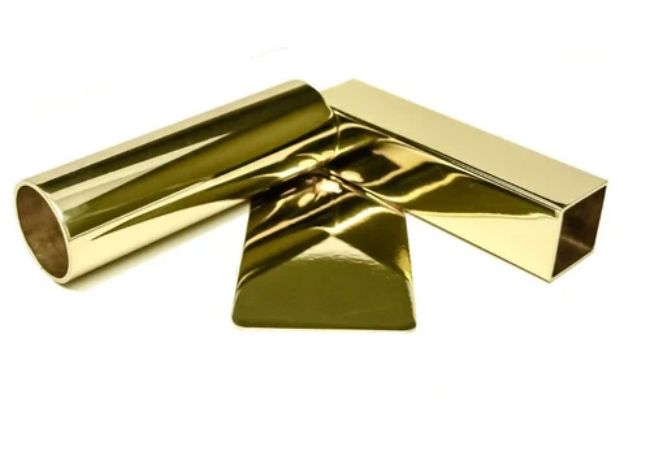
How to Electroplate Brass Parts
In conducting electroplating, you first clean the brass surface to eliminate any potential contaminants such as dust and other dirt. Thereafter, you subject the brass part into a bath containing chrome or nickel ions before incorporating a voltage.
The flow of electricity initiates the transfer of ions from the bath to the brass surface through an anodic process. You can vary the thickness of the coat by regulating the voltage parameters and process duration.
A secondary process can succeed the electroplating process to further enhance the finish. For instance, polishing can remove surface imperfections such as bumps and scratches resulting in an even finish.
Advantages of Electroplating Brass
Employing electroplating on brass surface has the following benefits to it:
- Augments brass’ durability by improving its resistance to impact, corrosion and wear. Plating nickel over your brass for instance results in a less porous finish with very high resistance to corrosion.
- Electroplating is applicable even on complex parts resulting in a uniform reach since it is chemically controlled.
- Enhances the appearance of the part or product especially where aesthetics is of concern.
- Using a chrome plating is certain to hold the plating longer by reducing the chance of delamination.
- Is an economical process when dealing with large volumes of small parts.
Limitations of Brass Electroplating
There are a few drawbacks in employing electroplating over brass surface as follows:
- Electroplating process leaves behind residue which is harmful to the environment making it difficult to properly dispose.
- The initial costs for setting up an electroplating system are highly prohibitive considering the equipment and materials needed.
- Undertaking the electroplating process takes time since the deposition process is typically slow. It is even slower when working on large brass pieces and intend to achieve thicker coating.
Uses of Brass Electroplating
Common uses of electroplating brass include:
- Brass pieces such as plumbing components like faucets and hardware equipment like pipes and handles employ electroplating to enhance appearance.
- You also find some musical brass instruments such as trombones and trumpets electroplated with metal such as chrome for enhanced appearance.
Antique Brass Surface Finish
Antique brass is a finishing that specially treats and colours the brass surface to give it a bucolic appearance. It is essentially the look that unpolished bronze will give when left over time.
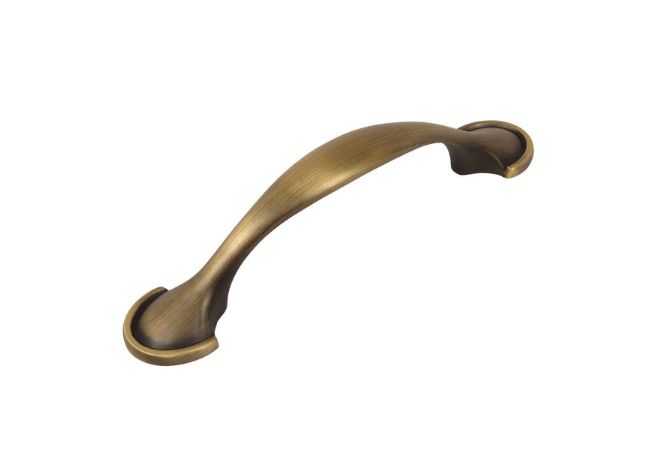
How to make Antique Brass Surface Finish
There are various shades that you can achieve with antique brass starting from a light shade to a deeper and darker hue. In creating an antique finish, you first clean the brass surface using a solvent to remove any contaminants.
An application of lacquer helps in tarnish protection which you can achieve by using multiple coats of the clear substance. The shade of the antique brass is capable of altering by varying the coating color and applications from rich brown to matte black.
Advantages of Antique Brass Surface Finish
Antique brass has the following advantages:
- It is a low cost finishing method given that it does not employ any special materials and equipment.
- The end result is aesthetically unique and pleasing giving a rustic feel.
- You have the option of different colour shades.
- Its reflectiveness pales in comparison with polished brass allowing you to conceal surface infractions.
Limitations of Antique Brass Surface Finish
Drawbacks to antique brass finish include:
- When used for equipment and parts out of a classical context, antique brass can look out of place.
- If the surface is not carefully treated, it can result in a patched finish.
Uses of Antique Brass Surface Finishing
Some common applications of antique brass are as follows:
- Use of antique brass is common for artefacts used in classical settings of interior design.
- Electrical fittings such as sockets and switches utilize antique brass finishing.
Satin Brass Surface Finishing
Satin brass finish is a textured surface treatment that involves lacquer application with a brush usually with a muted brownish hue.
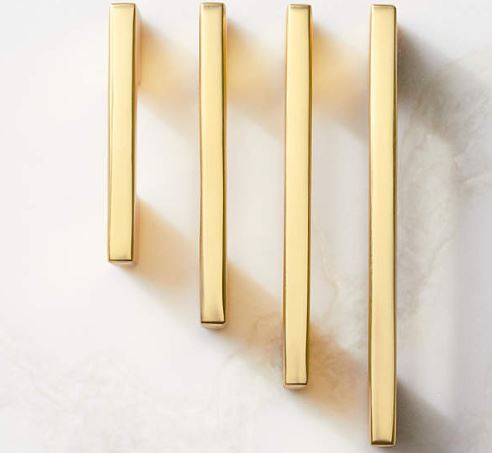
How Apply Satin Brass Finish
Before applying a satin finish, you have to polish the brass piece to smoothen the surface. Thereafter, you brush the surface with a special satin wheel which gives the surface its desired texture. The process ends by applying a coat of lacquer to secure the finish and safeguard the base.
Advantages of Satin Brass Surface Finish
A satin finish derives you the following benefits:
- The finish obtained is typically smooth and even.
- A satin finish conceals patches of water and fingerprints.
- The resulting surface after applying this finish is tarnish resistant.
- Brass with satin finish is highly durable capable of tolerating extreme temperatures.
Limitations of Sating Brass Surface Finish
- Since the process has manual elements, it is difficult to reach some surfaces for complex brass parts leaving patches unbrushed.
- The coat requires regular maintenance to prevent eventual tarnishing.
Uses of Sating Brass Fishing
- Jewelry pieces such as necklaces and bracelets.
- Light fixtures like bulb holders and chandeliers.
- Hardware implements and fittings like cabinet pulls and sockets.
Brushed Brass Surface Finish
While similar to satin finish, the brushstrokes in brushed brass are more pronounced enhancing the textured look. Consequently, upon coating, the outcome differs from a polished brass surface with its matte finish.

How to Achieve Brushed Brass Surface Finish
Application of brushed finish can either be manually done by hand or wheel-aided with the strokes applied in one direction. You can conduct brushed finish on an unsmoothed surface after the last machining process. Adding a clear coating allows you to protect the underlying surface.
Advantages of Brushed Surface Finish
- Brushed brass conceals surface patches and fingerprints.
- The resulting finish is highly durable.
- Maintaining the surface is easy.
Limitations of Brushed Brass Surface Finish
- The process of applying a brushed finish can be time consuming.
- Without a coating, the brushed brass surface can tarnish over time.
- Cannot be cleaned with solvents as it will damage the surface, instead use water.
Uses of Brushed Brass
- Light fixtures such as chandeliers and menorahs.
- Plumbing fixtures like taps.
- Hardware fixtures such as door knobs and handles.
- Cartridge casings for firearms.
Powder Coating Brass
Application of powder coating on brass is in a free-flow form without the need of liquidized binder and filler. The result is usually a coating superior to traditional paint in terms of toughness.
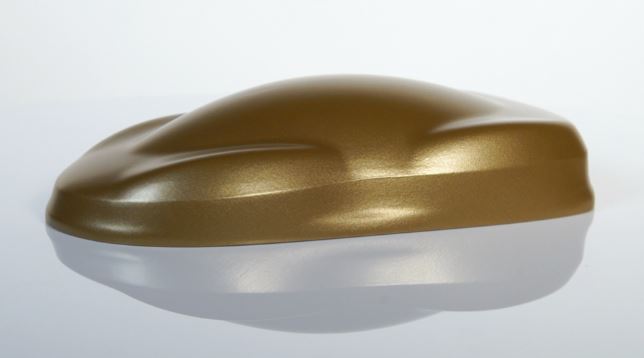
How to Powder Coat Brass
The application process of powder coating begins with cleaning the brass surface to eliminate any contaminants such as dirt and dust. Applying a powder coat over a poorly prepared surface can result in poor powder adhesion compromising the quality of finish.
Application of powder coating on brass is electrostatically through use of an electrostatic spray gun in a spray booth. Fluidized powder, typically thermoset polymer or thermoplastic, is fed into the gun where it is charged before deposition.
A curing process in an oven with temperatures between 160 and 230 oC follows. The duration can vary between ten to sixty minutes depending on the brass part size, shape and coating thickness.
Advantages of Powder Coated Brass
- Brass powder coating is solvent free and thus environmentally safe.
- You can achieve thicker coatings when using brass powder coating compared to conventional alternatives offering greater surface protection.
- Curing a powder coating on brass is faster in comparison with liquid based coatings.
- It is a cost effective and reliable process when conducted on a large scale.
Limitations of Powder Coating Brass
- The initial cost of setting up powder coating is high and uneconomical for small production runs.
- You can only use a limited range of materials for powder coating usually, thermoset polymer or thermoplastic.
- Producing consistently thin coatings with brass powder coating is difficult.
- The powder coating process is long considering the preparation, application and curing processes, and even longer for large brass parts.
Uses of Powder Coated Brass
- Used in coating hose couplings.
- Components such as gears, locks and hinges.
- Plumbing components and valves.
Brass Physical Vapor Deposition (PVD)
PVD entails a coating process where a thin coat is deposited over the brass surface in a vacuum. A PVD brass finish offers corrosion resistance, resistance to tarnish and preventing discoloration.
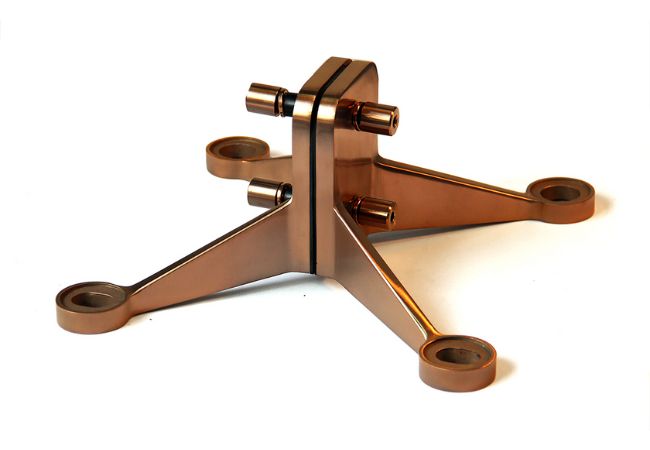
How to Apply PVD on Brass
There are different PVD methods available with the most common being evaporation and sputtering processes. In both processes, you observe transition of the material with a vapor phase sandwiching condensed phases.
There is evaporation or sputtering of the coating material which combines with a reactive gas like nitrogen forming the deposited compound. The coating is highly adherent forming a strong bond with the brass surface.
Advantages of Using PVD on Brass
- The resulting coating from PVD is hard offering impressive resistance, from impact, corrosion and abrasion.
- You can use a wide variety of materials as coating for your brass part whether organic or inorganic.
- When compared to other brass finishing, PVD’s effect on the environment is more tolerable.
- There are different methods at your disposal to apply physical vapor deposition on brass surface.
Limitations of PVD on Brass
- The initial cost of setting up a physical vapor deposition chamber is high given the equipment needs.
- Particular PVD methods are demanding given the high value temperatures and vacuums achieved requiring intricate cooling systems.
Uses of PVD Brass
- Architectural brass pieces.
- Brass sheeting and panels.
- Firearm casings.
- Jewelry pieces and watches.
Polished Brass
Polishing brass is an age old finishing option for brass items that is highly reflective with a yellowish-gold appearance.
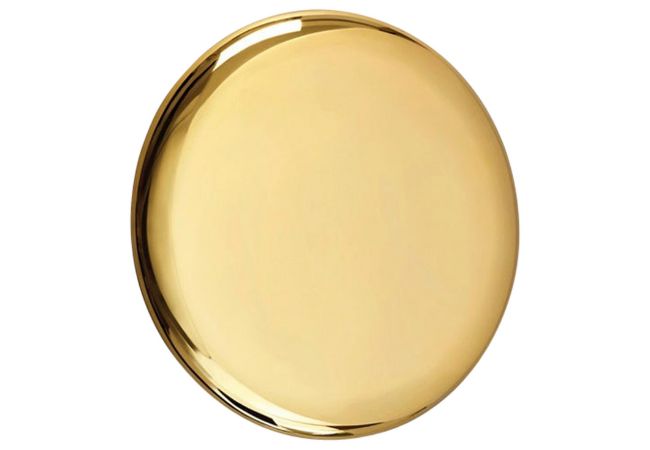
How to Polish Brass
The initial process in polishing brass fixtures is cleaning the surface for removal of any contaminants. Thereafter, you employ microfiber clothing or soft brush to achieve the polished look usually by repetitive action.
Advantages of Brass Polishing
- The appearance of polished brass has a high aesthetic appeal given its highly reflective finish.
- Treating the brass surface prior to polishing makes the process easy to perform.
- It is a low cost finishing technique.
Limitations of Polishing Brass
- While the surface of polished brass is impressively smooth, it easily reveals water patches and fingerprint markings.
- The polishing process is time consuming since it is manually undertaken especially when working on intricate pieces and many items.
Where to Use Polished Brass
- Plumbing fittings use in the bathroom.
- Household furniture items.
- Door and window fixtures such as handles, knobs and shutters.
Burnishing Brass
Burnishing brass is a finishing approach where you reduce the roughness of the brass surface. At the same time, you will remove imperfections on the brass surface.
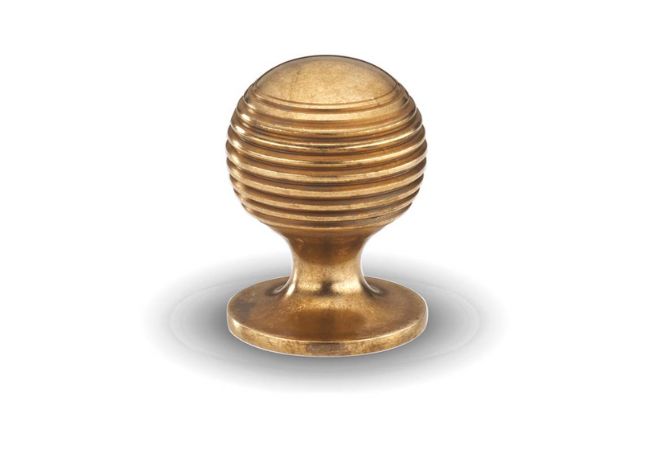
How to Burnish Brass
The burnishing process differs from brushing since while application in the latter is unidirectional, with the former it is circular. It is typically a two-step process beginning with manually polishing the surface and finally burnishing for a semi-polished look.
Advantages of Burnished Brass
- Reduces surface roughness of brass while enhancing hardness.
- Offers enhanced surface resistance to wear and corrosion.
- Has a reduced cycle time allowing use on many items.
- It is economical given the low costs involved with low energy demands.
Limitations of Burnishing Brass
- Burnishing on complex designs can be a challenging task.
- It is ineffective for rigid brass parts like pipe fixtures with thin walls.
Where to Use Burnished Brass
- Light fixtures such as bulb holders.
- Hardware fittings like door knobs.
- Utensils such as brass jars and kettles.
Waxing Brass
Involves applying wax over a brass surface giving it provisional protection over touch and the elements without concealing surface details. You can re-wax your brass item even it has undergone wear.
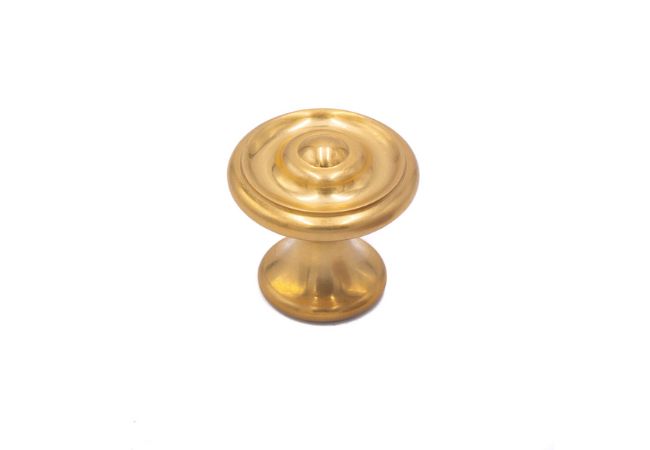
How to Wax Brass
The waxing process begins with preparation of wax free from synthetic components (e.g. polyethylene) that make removal challenging. Application of wax is typically done by brush wiping it over the brass surface before allowing evaporation of the solvent.
Once the wax sets, a buffing process to clean the surface facilitated by a soft cloth follows leaving a thin wax coat. You can always remove the wax later to undertake cleaning or implement another finish.
Advantages of Waxing Brass
- It is a low cost and economical method.
- The process of applying a wax finish on brass is simple and non-complicated.
- It takes a short time to implement this method.
- Suitable for living finishes where it offers temporal protection.
- It does not damage or alter the brass surface
Limitations of Waxing Brass
- It is a provisional finish and not meant for long term protective use.
- Restricted for internal use since it is easily susceptible to dust and patination.
- Requires regular maintenance to maintain the appearance.
Uses of Waxed Brass
- Indoor exhibition items such as brass artefacts.
- Furniture implements.
- Brass tools.
Patinated Brass
Patinated brass describes the appearance insinuating aging whether naturally arrived or chemically induced. Patination can occur over time on an exposed brass feature that lacks a lacquer coating and is unpolished.
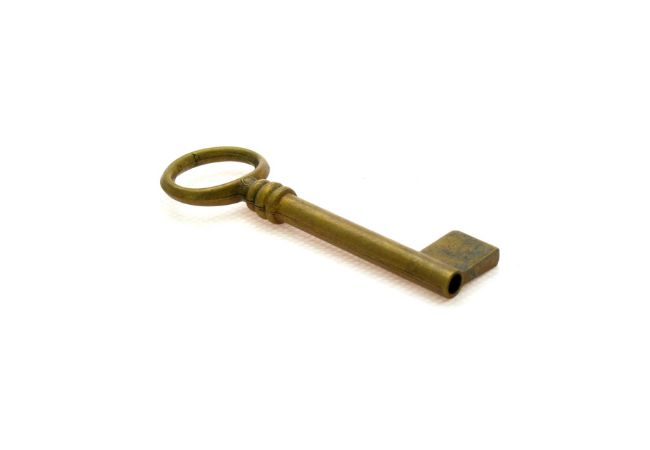
How to Apply Patina on Brass
Brass will patina when exposed to the elements such that the metal surface interacts with oxygen forming an oxide layer. The natural process takes time to achieve, usually years, giving the brass piece a brownish green hue.
Alternatively, you can initiate patinated brass by chemical process where you subject the part to ammonia treatment for instance. In this case, you submerge the brass piece in a concentrated solution of ammonia and salt initiating a change in hours.
Advantages of Patinated Brass
- A patina brass finish is highly attractive and pleasing to behold.
- Patina brass possesses anti–bacterial properties.
- This type of finish can tolerate extreme temperatures.
Limitations of Patinated Brass
- It takes a long time to occur naturally and involves a costly set-up to infuse artificially.
Uses of Patinated Brass
You can patinate almost any brass item such as:
- Hardware fixtures like door knobs and handles.
- Brass sculptures.
- Roofing material.
- Plumbing fittings.
Determining Cost of Brass Finishing
Determining the cost of your brass finishing is important to allow you operate within a profit margin. There are several variables to consider in brass finishing cost determination.
These include:
- Labor cost encompassing all the workforce needed to actualize the brass finishing.
- Production cost includes the set-up costs, energy requirements and other fixed costs.
- Product features such as design, output and finishing type.
- Post-production needs such as maintenance, rework or scrap.
Relevant News