Sheet Metal Fabrication Cost: Factors That Affect Cost and How to Reduce Cost
Upload Time:
Feb 25, 2024
Sheet metal fabrication is the art of transforming raw metal sheets into various components and structures, serving a multitude of industries. While you may already be well-acquainted with the basics, we will delve deeper into the nuances that impact the cost of your fabrication projects. The cost aspect extends beyond material and labor expenses; it encompasses an array of variables that, when managed effectively, can lead to significant savings.
Throughout this article, we will explore the cost elements, offering a step-by-step guide on calculating sheet metal fabrication expenses. We will also analyze how the quantity of parts can influence the unit cost, providing practical examples and highlighting the economies of scale at play. Following this, we’ll dive into the specific factors that exert their influence on fabrication costs, from material selection and design complexity to geographic location and production methods.
Our ultimate goal is to equip you with the knowledge and strategies necessary to reduce costs in your sheet metal fabrication projects while maintaining the highest standards of quality. Whether you’re a seasoned mechanical designer or a purchase officer seeking to optimize your procurement decisions, this article will provide valuable insights that can be applied in your day-to-day endeavors.
Understanding Sheet Metal Fabrication Costs
1. Planning the Workflow
When receiving a sheet metal design, the first step is to determine the manufacturing process, which entails deciding the order of operations. Typically, it starts with cutting, followed by arranging processes like bending, welding, riveting, and stretching in accordance with the design requirements. For more complex or larger projects, once the manufacturing process is decided, detailed process drawings for each step may be created. The primary cost in this phase primarily consists of labor costs for the process engineer. Good process engineers could foresee and avoid potential problems in the workflow, but they also cost more. A good engineer in China costs 10~30 USD/hour, based on the exchange rate and salary level in 2023.
2. Material Selection
With the production cycle established, the next step is to carefully select the appropriate sheet metal material. Factors such as material type, thickness, and quality must align with the project’s requirements. The right material choice not only affects the project’s feasibility but also plays a significant role in determining overall costs. The cost of materials is very simple.
Raw Material cost = Volume x Density x price/kg
For 1 USD/kg steel, for example, the density is 7.8 kg/dm3 (7800 kg/m3), and the plate dimensions are 1.2m x 2.4m x 2mm.
Raw Material cost = 1 USD x 7800x 1.2×2.4×0.002 = 44.928 USD
Note that even for the same material, a different gauge (thickness) sheet could have a different price per kg. So you have to repeat this calculation for all the different thicknesses and different materials.
3. Sheet Metal Cutting
Sheet metal cutting processes commonly include laser cutting, plasma cutting, and waterjet cutting. For certain high-volume products, punch and die cutting can also be applied. In laser cutting, plasma cutting, and waterjet cutting, engineers must create specific cutting programs, which are executed by CNC machinery. Similar to other CNC machining cost, the costs involved encompass labor and machinery depreciation. Most manufacturers employ a simplified cost calculation method, which factors in the unit time cost (comprising both labor and machinery depreciation) multiplied by the processing time required.
It’s important to note that, prior to processing any product, the machinery must be set up. While the setup for cutting machinery is relatively straightforward, it still involves tasks such as program input and parameter configuration. The total processing time should include both the setup time and the actual processing time. Therefore, for processing ‘n’ units of a product, the machining cost calculation becomes unit time cost x (setup time + ‘n’ x time per unit processing) / ‘n‘.
For larger production quantities that utilize die stamping for cutting, the cost estimation must also consider the expenses associated with producing the die molds. While the cost of dies should ideally be distributed across the total number of products throughout the die’s entire lifespan, during the initial stages of a product’s development, the ultimate lifecycle (in terms of quantity) remains uncertain. Consequently, in practical production scenarios, die costs may either be calculated separately when they are made or allocated into the unit product cost of the first batch. These costs are typically not factored into subsequent production batches. The machining cost calculation then becomes unit time cost x (setup time + ‘n’ x time per unit processing) / ‘n’ + die cost/’n’.
4. Bending and Stretching
Bending, primarily executed using a press brake, is the key process for shaping metal sheets into desired forms. Bending necessitates two essential tools: an upper convex punch that exerts pressure from above and a lower concave die that supports from below. However, when calculating the cost of the bending process, we typically exclude tooling or die production expenses. This is due to the fact that press brakes come equipped with a variety of commonly used bending tools. Hence, when determining the cost for the bending operation, we employ a methodology akin to other processes, factoring in machine setup time and multiplying it by an hourly rate, which includes labor and machine depreciation. Setting up a press brake, while slightly more complex than CNC cutting machinery, requires a slightly longer setup time. So the typical bending process machining cost estimation is:
unit time cost x (setup time + ‘n’ x time per unit processing) / ‘n’
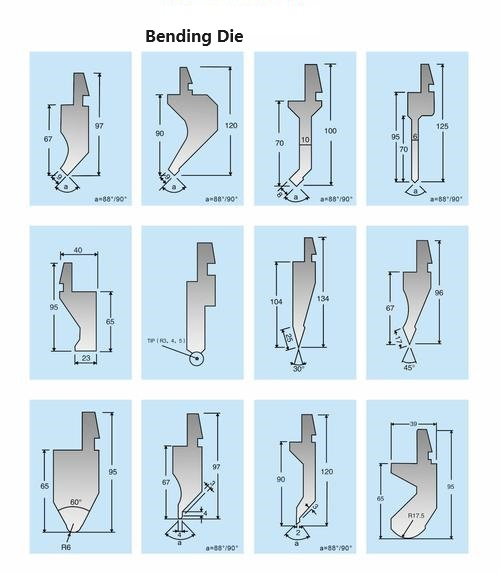
Press brakes arrive with an array of built-in tooling that caters to a broad spectrum of bending needs, including common angles like 135 degrees, 90 degrees, 45 degrees, 30 degrees, and 60 degrees. However, not every bending requirement can be met with off-the-shelf tooling. Situations arise, such as interference issues or the need for non-standard bending angles, where custom tooling becomes a necessity. In such cases, tooling costs must be factored into the sheet metal fabrication expenses.
Bending, unlike stretching, doesn’t alter the thickness of the metal sheet. Stretching, on the other hand, involves elongating the metal sheet, which does affect its thickness. A classic example of stretching is transforming an aluminum sheet into a beverage can. Stretching processes lack standard tooling, and thus, the cost of producing custom tooling must be considered for all stretching operations. So the typical die-needed bending and stretching cost estimate is:
unit time cost x (setup time + ‘n’ x time per unit processing) / ‘n’ + die cost / ‘n
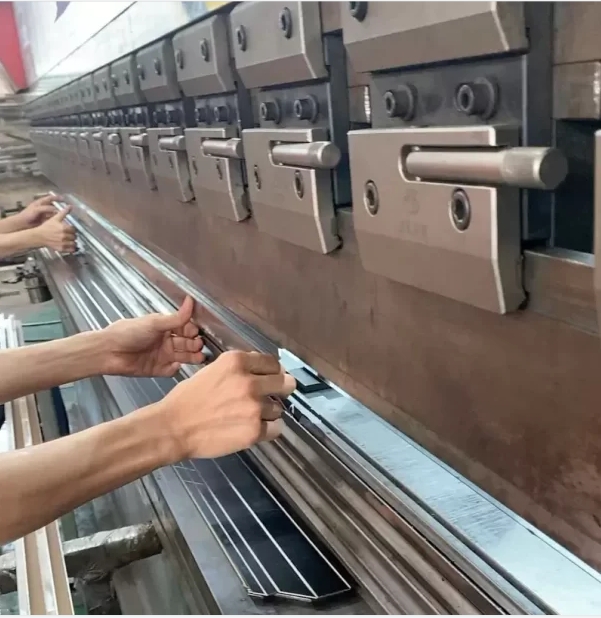
5. Welding and Riveting
Apart from automated welding for large-scale production, welding and riveting processes are labor-intensive. The primary cost factor is skilled labor, as the equipment required is typically relatively inexpensive and often negligible. In China, the hourly cost for skilled labor of this nature is approximately $10 to $15 (as of 2023). The cost calculation formula for such processes is hourly labor wage x processing time.
6. Coating, anodizing, passivation, painting, and other surface treatments
The detailed calculation for surface treatment fabrication can be rather intricate. Each type of surface treatment comes with its own unique cost factors, typically tied to variables like the weight, surface area, film thickness, quantity, and other specific characteristics of the product being treated. Some sheet metal components utilize pre-treated sheet materials, eliminating the need for post-processing, for example, when using phosphate steel sheets.
For the sake of simplicity, a common practice is to add an additional 5% to 15% to the sheet metal fabrication cost to account for surface treatment expenses. As a general rule, processes like black oxide, anodizing, and passivation tend to be more cost-effective, whereas electroplating, painting, and powder coating are often more expensive. Unusual surface treatments, such as Teflon coating or precious metal plating, would necessitate separate cost calculations.
7. Administration Cost
Every sheet metal fabrication facility requires administrative staff, such as accountants, business personnel, and management professionals. These costs fall under the category of administration expenses. A simplified method for calculating these costs is to add approximately 20% to 30% to the overall expenses for administrative overhead.
Implicit in this approach is the assumption that “non-production” personnel typically make up about 20% to 30% of the total workforce in most manufacturing facilities. The proportion allocated for administrative costs may vary, with smaller sheet metal fabrication companies calculating it on the lower end and larger enterprises on the higher end of this range.
8. Packing and Shipping
Sheet metal components are relatively delicate and often require a high standard of appearance, making their packaging requirements quite stringent. It’s essential to ensure that they remain unscathed during transportation, staying protected even in the event of impacts. Estimating the cost of packaging can be challenging, as it depends on various factors such as the shipping distance, method, component specifications, weight, structural strength, and more.
Transportation costs are similarly intricate. Sheet metal parts are typically considered “bulky cargo,” meaning they have a lower gross weight density. As a result, shipping costs are usually calculated based on volume rather than weight. Costs can vary significantly based on the shipping distance, mode, and the overall quantity (volume or weight) being transported. Shipping a full container load (FCL) by sea is considerably cheaper than container load (LCL) shipping by sea.
Naturally, international express services are pricier than air freight, which, in turn, is more expensive than sea freight. As a rough estimate, packaging and transportation costs for international express typically amount to around 12% to 15% of the production cost, while sea freight costs are typically within 5% or less of the production cost.
9. Estimation of “unit time cost”
You may have noticed that the term “unit time cost” appears repeatedly in the cost calculations mentioned above. But how is it estimated? “Unit time cost” generally refers to the machine hourly cost (for instance, a CNC laser cutting machine). This cost encompasses both the machine’s depreciation and labor expenses. A simplified way to calculate it is by dividing the machine‘s purchase cost by 2,000 hours.
For example, if a piece of equipment costs $25,000, the estimated cost per hour is roughly $25,000 divided by 2,000, which equals $12.5 per hour. The implicit assumption here is that the equipment depreciates over a period of approximately two years, along with the associated labor costs.
10. Quantity Matters the Most
Similar to other manufacturing processes, batch size has a substantial impact on the unit cost of sheet metal parts, and this influence manifests in three primary ways:
-
Setup and Tooling Costs: As evidenced in the preceding calculations, setup costs represent a significant portion of the overall expenses. Importantly, these setup costs do not scale linearly with batch size. Whether producing 10 parts or 1000, the setup occurs just once, but the allocation per unit part differs by a factor of 100. The same principle applies to tooling costs.
-
Process Variation: Varying batch sizes necessitate different manufacturing processes. For example, laser cutting is the preferred method for a few dozen parts, whereas larger quantities may benefit from cost-efficient die stamping. With even greater quantities, automated production becomes feasible, further reducing the unit cost.
-
Skill and Optimization: In high-volume production, worker expertise tends to increase as they gain experience. This experience allows for the refinement of process parameters, leading to lower unit costs. In general, for the same part, the unit cost for a batch of dozens can be several times higher than a batch of thousands. Batch size remains one of the most pivotal factors affecting costs.
How to Reduce Sheet Metal Fabrication Costs
Here are some tips to reduce sheet metal fabrication costs.
1. Choose the right raw material
In principle, in order to reduce the raw material costs, opting for lighter, lower-hardness, and more ductile metal sheets is cost-effective, provided they offer sufficient strength. For example, between a 2mm aluminum sheet and a 2mm stainless steel sheet, if both provide the required strength, the 2mm aluminum sheet is the more economical choice.
When dealing with sheet metal fabrication parts that involve bending or stretching, the material’s heat treatment status becomes a consideration. T6-state aluminum sheets are exceptionally challenging to bend and prone to fracturing, while annealed aluminum sheets are more pliable.
In cases where welding is necessary, the material’s weldability should also be factored in. Thin aluminum sheets are relatively challenging to weld, which can increase the cost of the welding process. On the other hand, welding steel sheets tends to be more cost-effective.
If welding isn’t required and there are no stringent surface appearance requirements, it’s advisable to opt for pre-treated sheet materials. This eliminates the need for post-fabrication surface treatments. Examples of such materials include galvanized steel sheets or anodized aluminum sheets. This not only simplifies the process but also reduces overall costs.
2. Use a Common Gauge (Thickness) of Sheet Metal
When designing sheet metal parts, it’s advisable to use readily available sheet thicknesses in the market. Different countries and regions have varying standards for sheet metal thickness. For instance, if you’re planning to manufacture in the United States, sheet metal thickness is commonly measured in gauges, with common values like 12, 14, 16, and 18-gauge. On the other hand, if you intend to produce in China, sheet metal thickness is typically measured in metric units, such as 2mm, 3mm, 4mm, 5mm, 10mm, and so on.
Unless you’re producing a very large quantity of parts, customizing a special thickness of sheet metal can be costly and may not be a practical choice. Therefore, it’s generally more cost-effective and practical to work with the standard thicknesses readily available in the region where your manufacturing will take place.
3. Avoid Complex Design Features
The complexity of your design often correlates with higher costs. Parts that involve numerous cuts, bends, and welds tend to come with increased expenses. While intricate design elements may enhance aesthetics, they also substantially elevate costs. In most cases, simplicity is a prudent goal. Hence, it’s advisable to opt for straightforward angle bends to reduce fabrication expenses. These bends should have inside radii equal to the thickness of your chosen material.
Using small bends on large, thick components can lead to inaccuracies, so it’s best to avoid them. Maintaining consistency in your bend radii is another way to enhance cost-efficiency during fabrication. Additionally, refrain from incorporating features like blind holes, machined pockets, or chamfered edges unless they are essential. These features often extend lead times and increase manufacturing costs. A reliable sheet metal design guide will assist you in making the most cost-effective decisions for your sheet metal products.
4. Weigh the Choice of Surface Treatment
When contemplating surface treatment, it’s essential to take a comprehensive approach, considering factors such as appearance requirements, weather resistance, and cost implications. The choice of finishing for sheet metal often hinges on a range of considerations, including the part’s intended use and its aesthetic demands.
For example, pre-plated metals might be cost-effective for a normal environment. However,pre-plated metals like galvanized options may not be the most suitable choice if your design involves welded seams. It’s also prudent to postpone finishes like engraving and silkscreening until the later stages of product development.
Some raw materials inherently possess resistance to corrosion, obviating the need for overly specialized finishes. Specialized finishes can sometimes necessitate cost estimators soliciting external quotes, thereby increasing both costs and lead times. On the contrary, several common finishes are not only more cost-effective but also quicker to implement. Examples include chrome plating, passivation, anodizing, and powder coating, which are readily available with minimal cost impact.
5. Talk with Sheet Metal Professionals
Sheet metal fabrication is a craft that thrives on accumulated expertise. Seeking advice from experts in the early stages of part design can significantly reduce manufacturing costs. Designers can steer clear of features that may be challenging or even impossible for sheet metal fabrication or avoid unnecessary redundancy in their designs.
6. Other Advice
-
Adhere to Appropriate Tolerances: Parts with numerous features that require tight tolerances often lead to increased costs. These tolerance specifications encompass parameters like radii, distances, and hole diameters. Since only a select few surfaces are critical to a part’s functionality, it is prudent to allocate precise tolerances to those surfaces. By limiting the use of tight tolerances, your design becomes more budget-friendly.
-
Optimize Bend Radius: Another straightforward approach to economizing in sheet metal fabrication is to incorporate optimal geometries into your part design. The internal bend radius should ideally fall within the range of 0.030 inches and 1x the material thickness. This enables manufacturers to efficiently create the required radii using specialized tools tailored to these geometries.
-
Embrace Efficient Fasteners: Employing extravagant fasteners for your sheet metal projects can inflate costs and hinder the manufacturing process. Therefore, it is advisable to favor swift, economical, and readily available fastening solutions.
Conclusion
In conclusion, understanding the intricacies of sheet metal fabrication costs and the various factors that influence them is essential for achieving cost-effective and efficient manufacturing. By taking a thoughtful approach to design, material selection, surface treatments, and other critical considerations, it is possible to reduce expenses while maintaining the quality and functionality of your sheet metal components. Collaboration with experienced professionals and adhering to best practices can further enhance cost-efficiency in sheet metal fabrication. Remember that even small design and process optimizations can lead to significant cost savings, making your sheet metal projects more competitive and successful.
Relevant News